Welke tests voor PCB?
Inhoudsopgave
Welke testen zijn nodig voor PCB productie?
In het fabricageproces van elektronische producten is de kwaliteit van PCB's (Printplaat) bepaalt rechtstreeks de prestaties en betrouwbaarheid van het eindproduct. Er kunnen honderden componenten en duizenden soldeerverbindingen op een printplaat zitten en kleine defecten kunnen ervoor zorgen dat het hele systeem uitvalt. Het is erg belangrijk om de productkwaliteit te garanderen, de productiekosten te verlagen en de concurrentiepositie op de markt te verbeteren.
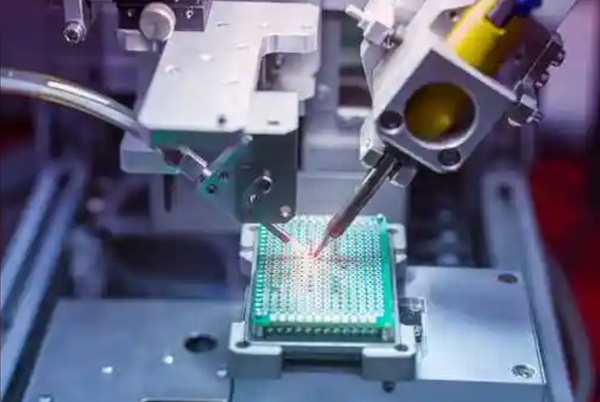
De voordelen van PCB-tests
PCB-testen zijn een cruciaal onderdeel om de kwaliteit en betrouwbaarheid van printplaten te garanderen
- Vroegtijdige opsporing van ontwerpfouten: Uitgebreide tests identificeren functionele en maakbaarheidsproblemen in PCB's, zodat ontwerpers tijdig aanpassingen en optimalisaties kunnen doorvoeren.
- Aanzienlijke kostenreductie: Het ontdekken van problemen tijdens de prototypefase bespaart meer dan 90% van de kosten in vergelijking met het identificeren van problemen na de massaproductie, waardoor catastrofale uitval van batches wordt voorkomen.
- Kortere marktintroductietijd: Het snel opsporen van hoofdoorzaken versnelt ontwerpiteraties, waardoor volwassen producten sneller kunnen worden gelanceerd dan bij concurrenten.
- Verbeterde merkreputatie: Het verlagen van het retourpercentage tot minder dan 1% verbetert de klanttevredenheid en vergroot de geloofwaardigheid van de markt.
- Verzekerde veiligheid: Voorkomt ongelukken zoals brand of elektrische schokken veroorzaakt door printplaatdefecten en beschermt gebruikers’ levens en eigendommen.
Waar worden PCB's voornamelijk op getest?
Het doel van PCB testen en inspecteren is om de prestaties van PCB's te vergelijken met standaard printplaten.Het zorgt ervoor dat alle PCB fabricageprocessen goed functioneren en zonder defecten volgens de projectspecificaties. Een PCB bestaat uit verschillende elementen, componenten, die elk de algemene prestaties van het elektronische circuit beïnvloeden. Deze elementen worden in detail geanalyseerd om de PCB-kwaliteit te garanderen en de betrouwbaarheid van het product te verbeteren.
1. Kwaliteit poriewand
Gatenwanden worden meestal geanalyseerd in omgevingen met cyclische en snelle temperatuurveranderingen om hun reactie op thermische effecten te begrijpen.Dit zorgt ervoor dat de vias niet barsten of delamineren wanneer de PCB in gebruik wordt genomen, waardoor de PCB zou kunnen falen.
2.Verkoperen
Koperfolies op printplaten worden op de printplaat aangebracht om voor elektrische geleiding te zorgen.De kwaliteit van het koper wordt getest en de treksterkte en rek worden in detail geanalyseerd om er zeker van te zijn dat het circuit soepel is.
3.Netheid
De zuiverheid van een printplaat is een maatstaf voor het vermogen van de printplaat om omgevingsfactoren zoals verwering, corrosie en vochtigheid te weerstaan, waardoor de printplaat langer meegaat.
4.Soldeerbaarheid
Soldeerbaarheidstests worden uitgevoerd op materialen om ervoor te zorgen dat componenten stevig op de printplaat bevestigd kunnen worden en om soldeerdefecten in het eindproduct te voorkomen.
5.Elektrische testen
Geleidbaarheid is essentieel voor elke PCB, net als de mogelijkheid om de minimale lekstroom van de PCB’ te meten.
6.Omgevingstesten
Dit is een test van de PCB’s prestaties en kwaliteitsveranderingen bij gebruik in een vochtige omgeving. Gewichtsvergelijkingen worden meestal gemaakt voor en na het plaatsen van de PCB in een vochtige omgeving en als het gewicht aanzienlijk verandert, wordt het beschouwd als schroot.
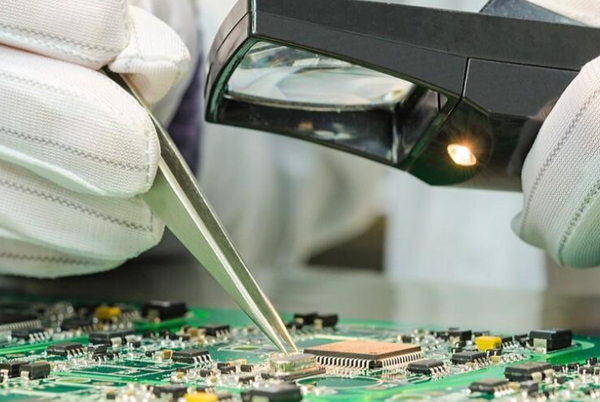
8 Belangrijkste testmethoden bij de productie van PCB's
1. Visuele inspectie
De meest elementaire detectiemethode is visuele inspectie. Hiervoor moeten ervaren technici duidelijke oppervlaktedefecten onderzoeken met behulp van loepen of microscopen (meestal een vergroting van 5-10x).
Belangrijkste inspectiepunten:
- Padoxidatie en -vervuiling
- Volledig circuit etsen, controleren op open of kortsluiting
- Gelijkmatige dekking van het soldeermasker, controleren op luchtbellen of afschilferen
- Juiste plaatsing en polariteit van componenten
- Soldeerverbinding glanzend en vormvast volgens normen
Voordelen: Extreem lage kosten, geen speciale apparatuur nodig, geschikt voor bedrijven van alle groottes.
BeperkingenHandmatige inspectie is traag (~2-5 minuten/bord), detecteert slechts ~70% van de oppervlaktedefecten, is ineffectief voor verborgen soldeerverbindingen zoals BGA's en is sterk afhankelijk van de ervaring en conditie van de operator.
2.Geautomatiseerde optische inspectie (AOI)
AOI-systemen gebruiken hogeresolutiecamera's (tot 50 µm precisie) om PCB-beelden vast te leggen vanuit meerdere hoeken.Beeldverwerkingsalgoritmen vergelijken deze met standaardsjablonen om de meeste defecten in de oppervlaktemontage te detecteren.
Typische detectiemogelijkheden:
- Ontbrekende, verkeerde of omgekeerde onderdelen
- Te veel of te weinig soldeer
- Opgeheven sporen, grafschennis
- Abnormale diameter of steek van de soldeerkogel
- Onjuiste markeringen of zeefdruk
Technische parameters:
- Inspectiesnelheid: 0,5-2 seconden/bord
- Minimaal detecteerbare grootte: 0201 onderdelen (0,6×0,3 mm)
- Vals alarm: <3%
Aanbeveling voor implementatie: AOI moet worden ingezet bij twee kritieke stations-post-reflow en post-golfsolderen en worden geïntegreerd met SPC-systemen voor real-time procesaanpassing.
3.In-circuit test (ICT)
ICT gebruikt aangepaste spijkeropstellingen om contact te maken met vooraf gedefinieerde testpunten op printplaten en verifieert de elektrische parameters van elke component met een >95% foutendekking.
De testonderdelen omvatten:
- Tests kort/open circuit
- Weerstands-, capaciteits- en inductiemetingen
- Controle van de polariteit van diodes/transistors
- IC-vermogensstroomcontroles
- Connector continuïteitstests
Configuratie apparatuur:
- Testkanalen: 512-2048
- Meetnauwkeurigheid: 0,1%-0,5%
- Testspanning: 5V-250V
- Testsnelheid: 3-10 seconden/kaart
Economische analyse: Inrichting kost ~$5.000-$20.000, geschikt voor stabiele ontwerpen met een maandelijkse productie van >5.000 eenheden, waarbij de ROI meestal binnen <6 maanden wordt behaald.
4.Vliegende sondetest
Flying probe testers gebruiken 4 tot 8 programmeerbare bewegende tasters in plaats van traditionele opspanningen, ideaal voor productie in kleine aantallen en met een hoge mix.
Technische kenmerken:
- Testdekking: Tot 98%
- Minimale testafstand: 0,2 mm
- Testsnelheid: 30-120 seconden/bord (afhankelijk van complexiteit)
- Capaciteitsbereik: 0,1pF-100μF
- Nauwkeurigheid weerstand: ±0,5%
Typische toepassingen:
- Verificatie van prototypes van nieuwe producten
- Borden met hoge betrouwbaarheid (militair/lucht- en ruimtevaart)
- Hoogwaardige producten in kleine volumes (medische apparatuur)
- Ontwikkelingsfasen met frequente ontwerpwijzigingen
Laatste ontwikkelingen: Moderne vliegende sondetesters integreren 3D laserhoogtemetingen voor het inspecteren van coplanariteit, soldeerpastadikte en andere mechanische kenmerken.
5.Geautomatiseerde röntgeninspectie (AXI)
AXI maakt gebruik van differentiële röntgenabsorptie door materialen om verborgen soldeerverbindingen zoals BGA's en QFN's te inspecteren.
Matrix detectievermogen:
Type defect | Detectiegraad | Percentage valse alarmen |
---|---|---|
Soldeerbruggen | 99 | <1% |
Ontlediging | 95% | 5% |
Onvoldoende soldeer | 98% | 2% |
Component verschuiving | 99% | 1% |
Uitrustingselectiegids:
- 2D AXI: Voor eenvoudige BGA-inspectie, ~$150.000
- 3D AXI:Laag-voor-laag beeldvorming, vanaf $300.000
- CT-scannen: 3D volumetrische gegevens voor storingsanalyse, >$500,000
6.Inbrandtest
Burn-in screent vroegtijdige defecten door versnelde stressomstandigheden. Gebruikelijke methoden zijn onder andere:
Temperatuurcycli-40°C~+125°C, 50-100 cycli
Burn-in bij hoge temperatuur: 125°C aangedreven werking gedurende 96 uur
Spanning: 1,5× nominale spanning gedurende 48 uur
Vochtigheidstest: 85°C/85%RH gedurende 1000 uur
Gegevensanalyse: Weibull-distributiemodellen voorspellen de levensduur van producten, waarbij MTBF>100.000 uur meestal vereist is.
7.Functionele test (FCT)
FCT simuleert echte gebruiksomgevingen om de volledige functionaliteit van de kaart te valideren.Testsystemen omvatten meestal:
- Programmeerbare voedingen (0-30V/0-20A)
- Digitale multimeters (6,5-cijferig nauwkeurig)
- Functiegeneratoren (100 MHz bandbreedte)
- Digitale I/O-modules (64-256 kanalen)
- Belastingbanken (simuleren werkelijke belastingen)
Essentiële testontwikkeling:
- Testplannen maken op basis van productspecificaties
- Ontwerp testopstellingen en interface-adapters
- Geautomatiseerde testscripts ontwikkelen (LabVIEW/Python)
- Criteria vaststellen voor slagen/niet-slagen
- Systemen voor gegevenstraceerbaarheid integreren
8.Grenswaarde scantest
Gebaseerd op de IEEE 1149.1 standaard, maakt gebruik van chips’ ingebouwde testcircuits om interconnecties te controleren, speciaal geschikt voor high-density boards.
Voordelen:
- Geen fysieke testpunten nodig
- Kan de onderste BGA-pennen testen
- Ondersteunt Flash-programmering en CPU-debugging
- Bereikt ~85% testdekking
Typische gereedschapsketen:
- BSDL-bestandsvalidatie
- Testvector genereren
- Software voor resultaatanalyse
- Testintegratie op systeemniveau
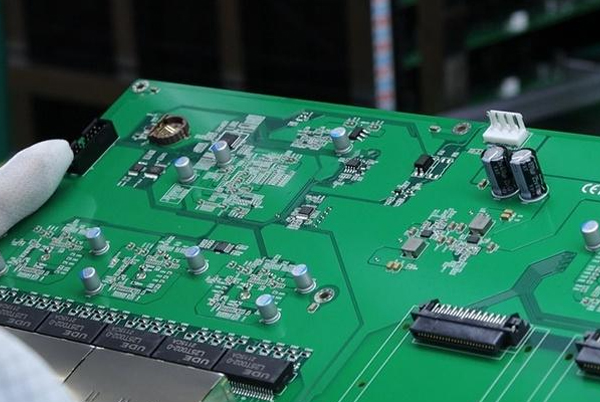
Vijf veelvoorkomende PCB-testuitdagingen & oplossingen
V1: Hoe breng je de testkosten in balans met de kwaliteitseisen?
A: Gefaseerd testen implementeren - basis AOI+FCT voor alle printplaten, AXI-sampling (10-20%) toevoegen voor kritieke producten en 100% inspectie voor militaire/medische toepassingen. Statistieken tonen aan dat deze combinatie defect escape rates <200ppm handhaaft terwijl de testkosten onder 5% van de totale productkosten blijven.
V2: Moet bij productie van kleine volumes gebruik worden gemaakt van ICT-tests of tests met een vliegende taster?
A: Een vliegende taster is voordeliger voor batches <500/maand.Praktijkvoorbeelden laten zien dat voor orders van 300 eenheden/maand de totale kosten van de vliegende taster (afschrijving + arbeid) ongeveer 1/3 zijn van ICT, met een productwisseltijd die teruggebracht is van 8 uur naar 30 minuten.
V3: Hoe kan ik de kwaliteit van BGA-soldeer effectief inspecteren?
A: Aanbevolen aanpak in drie fasen:3D AXI voor soldeervorm/overbrugging, grensscan voor elektrische connectiviteit, dan functionele test voor werkelijke prestaties. Een fabrikant van telecomapparatuur bracht met deze methode het aantal BGA-fouten terug van 1,2% tot 0,05%.
V4: Hoe kun je valse testfouten verminderen?
A: Houd het percentage valse alarmen onder de 2% door:
- De parameters van het AOI-algoritme optimaliseren
- Dynamische referentiesjablonen maken
- Classifiers voor machinaal leren implementeren
- Verificatiestations voor verdachte resultaten toevoegen
- Regelmatige kalibratie van apparatuur
V5: Hoe gebruik je testgegevens voor procesverbetering?
A: Zorg voor traceerbaarheidssystemen voor testgegevens met belangrijke stappen:
- Unieke ID's toewijzen aan elke PCB
- Alle ruwe testgegevens vastleggen
- CPK-analyse uitvoeren met Minitab
- SPC-controlediagrammen maken voor belangrijke parameters
- Regelmatig vergaderingen over kwaliteitsverbetering houden
Conclusie
PCB-test is om ervoor te zorgen de betrouwbaarheid van elektronische producten is een belangrijke schakel, en moet worden gebaseerd op productkenmerken, productie schaal en kosten budget om een redelijke testprogramma te ontwerpen. Door middel van de wetenschappelijke en systematische teststrategie, kunnen bedrijven de PCB failure rate van 50 delen per miljoen of minder, die het concurrentievermogen van het product markt en merkreputatie kan verbeteren controle!
Verwante berichten