Description
In the aerospace industry, the choice of materials and components for circuit boards (PCBAs) is not a matter of chance. Imagine that these electronic devices have to go through the rocket launch of severe vibration, extreme temperature changes in space, and a strong radiation environment; ordinary materials simply can not withstand this “torture”.
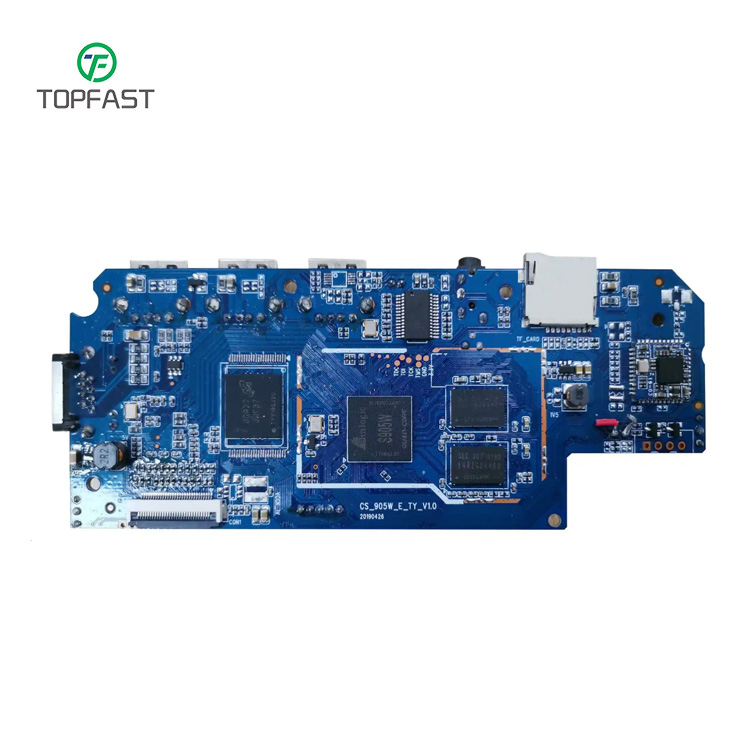
PCBA Basic Guidelines
1.PCB substrate
Aerospace circuit board substrate must meet the four diamond standards:
High-temperature resistance: to withstand extreme cold to the heat of repeated torture
Corrosion resistance: all kinds of radiation and chemicals in space can not hurt it a little bit
Good insulation: signal transmission must be stable and reliable
Sturdy and durable: it can’t be broken even by the violent vibration during the launching.
Commonly used “space-grade” materials include:
Polyimide (PI): like a “bulletproof vest” for circuit boards, it is particularly resistant to high temperatures.
Cyanoacrylate (CE): a well-balanced “top performer”.
Ceramic substrate: first-class heat dissipation performance of the “cooling expert”.
2.Component selection
1. chip (IC) how to choose?
Recognize the certification: QML-V/QML-Q certification is the “work permit”.
Anti-radiation design: cosmic rays should have the “Golden Bell Mask”.
Do not seek the latest but the most stable: 65nm or more mature process is more reliable
2. Passive components
Capacitors: Tantalum capacitors are the main force, ceramic capacitors should be COG/NPO type.
Resistors: film resistors are the first choice, metal foil resistors have the best performance.
Inductors: ferrite core or air core inductors are the most reliable.
3. Connectors
Standard: MIL-DTL-38999/32139 is the basic requirement.
Gold plating: Contacts must be plated with at least 50 micro inches of gold.
Double insurance: must be with secondary locking mechanism
3.Special Processes
Encapsulation technology
Ceramic package is the first choice, like a “spacesuit” for the chip.
Plastic packages must be certified by the military
BGA packages should not be used unless specially reinforced
Soldering
Traditional high Pb solder (Sn63Pb37) still dominant
If lead-free process is used, additional verification is required
X-ray “checkup” after soldering to make sure there are no “internal injuries”.
Protective treatments
Coatings must comply with military standard MIL-I-46058.
Parylene coatings are most effective
The thickness of the coating should be controlled within the range of the thickness of a hair.
4.Supply Chain Management
Purchasing Channel
Only take goods from the original factory or authorized distributors
Resist counterfeit components
Each component should have an “ID card”, the whole process can be traced.
Quality Inspection
100% inspection of incoming materials, no one can be left out
Random disassembly testing, no less than 10%.
Accelerated aging test to predict the service life
Change management
Any change must be re-verified
Changing components equals to re-certification
All change records should be kept completely

Aerospace PCBA soldering process
1.Soldering Process
In the aerospace field, an unqualified solder joint can be the “Achilles heel” of the entire mission. As the equipment has to experience repeated “torture” from extreme cold to extreme heat, the welding process must be foolproof.
1. Welding process: three big diamonds
Wave soldering: suitable for high-volume through-hole component welding, like a roller coaster, with the PCB passing through the molten solder
Reflow soldering (mainstream choice): accurate “local heating” technology, especially suitable for chip components
Selective wave soldering: “Precision spot soldering” technology for specific solder joints.
2. Reflow process
Temperature profiles are key: like baking a cake, too high a temperature will burn, too low a temperature will undercook it
Parameter customization: different materials and components require different “cooking solutions”.
Solder paste selection: to choose the special formula for aerospace-grade, ordinary solder paste simply can not carry the space environment
2.Aviation-grade circuit board processing
1. Precision control: the ultimate pursuit of micron-level
Laser positioning: accuracy of ± 5 microns (equivalent to 1/10 of a hair)
Optical alignment: Angular error less than 0.001 degrees (more accurate than a compass)
Surface treatment: copper foil smoothness comparable to mirror (Ra≤0.3μm)
2. Reliability Verification: Tougher tests than the space environment
Temperature torture test: -65℃ to 150℃ repeatedly tossed 1000 times
Vibration test: simulate the violent vibration of a rocket launch
Vacuum test: 10-⁶ torr vacuum under the extreme test
Aging test: 85 ℃ / 85% humidity under the continuous “sauna” for 1000 hours
3.Quality Control
Process monitoring: real-time monitoring of each key parameter like a medical checkup.
Traceability system: each board has an “ID card”, and the whole process can be traced.
Certification standards: meet the most stringent aviation quality standards (AS9100D, etc.)
4.S pecial Process
Microporous Processing: Laser-punched holes thinner than a hairline (±10μm precision).
High-frequency signal processing: impedance control accurate to ±3% (comparable to laboratory instruments)
Three-stage inspection: self-inspection + inspection + final inspection, to ensure that nothing is lost.
## Aerospace PCBA Surface Finishes
In the space environment, circuit boards face challenges far beyond those of terrestrial applications. To ensure reliable long-term operation, special “protection suits” must be used:
1. Metal protective layer (anti-corrosion treatment)
Electroless nickel/impregnated gold (ENIG): like a “golden armor” for circuits, it protects against rust and ensures good conductivity.
Electroless nickel/gold plating (ENEPIG): more advanced “composite armor”, especially suitable for high reliability requirements.
Characteristics: anti-oxidation, corrosion resistance, to ensure that the connector contact remains as new.
2.Organic protective layer (all-round protection)
Polyimide (PI) coating: aerospace-grade “protective clothing”, high temperature resistance up to 300 ℃ or more
Silicone potting: sensitive circuits to wear “anti-vibration airbag”, buffer mechanical shock
Effect: moisture-proof, shock-proof, radiation-proof, triple protection in one step.
Rigorous product testing
1. Environmental Adaptability Test
Temperature endurance race:
High and low temperature cycle (-65℃~150℃ repeated tossing)
Temperature shock (instantaneous switching of extreme temperatures)
Mechanical strength test:
Vibration test (simulate the violent vibration of a rocket launch)
Shock test (1500G acceleration shock)
2. Electrical performance verification
Flying needle test: like a “master acupuncturist” to accurately detect each node
Test Rack Verification: Comprehensive “physical examination” to ensure that all functions are normal.
Signal integrity: high-frequency signal transmission quality analysis
3. Accelerated aging test
Life Prediction: Accelerated aging through a high temperature and high humidity environment.
Continuous monitoring: record the trend of performance parameters
Failure analysis: Use an electron microscope to find out potential defects.
In conclusion, the special process requirements of aerospace PCBA are reflected in material selection, welding process, surface treatment, protective measures and test verification, and other aspects. Only by strictly following these requirements and constantly carrying out technological innovation and process improvement can we manufacture PCBA products to meet the needs of the aerospace field.