A Tecnologia de Montagem em Superfície (SMT) representa o núcleo da montagem eletrónica moderna, transformando os tradicionais componentes discretos através de orifícios em dispositivos compactos com pastilhas sem chumbo ou com chumbo curto montados diretamente nas superfícies das placas de circuitos impressos. Esta tecnologia permite a montagem de produtos electrónicos de alta densidade, altamente fiáveis, miniaturizados e económicos, apoiando simultaneamente processos de fabrico automatizados.
Visão geral da tecnologia de montagem em superfície
A tecnologia de montagem em superfície (SMT) revolucionou o fabrico moderno de produtos electrónicos, substituindo os volumosos componentes com orifícios de passagem por dispositivos compactos, sem chumbo, que são montados diretamente em placas de circuitos impressos.Sendo o processo de montagem dominante na indústria, a SMT permite a produção automatizada de dispositivos electrónicos de alta densidade, ultra-confiáveis e miniaturizados a custos reduzidos. Esta tecnologia transformadora tornou-se omnipresente em sistemas informáticos, equipamentos de comunicação e inúmeros produtos electrónicos, com a sua adoção a continuar a expandir-se à medida que a utilização tradicional de componentes através de orifícios diminui. O avanço contínuo dos processos e componentes SMT estabeleceu-a firmemente como a norma de ouro na montagem de produtos electrónicos, impulsionando a inovação ao mesmo tempo que satisfaz a procura crescente de dispositivos electrónicos mais pequenos, mais potentes e mais económicos em todos os sectores do mercado.
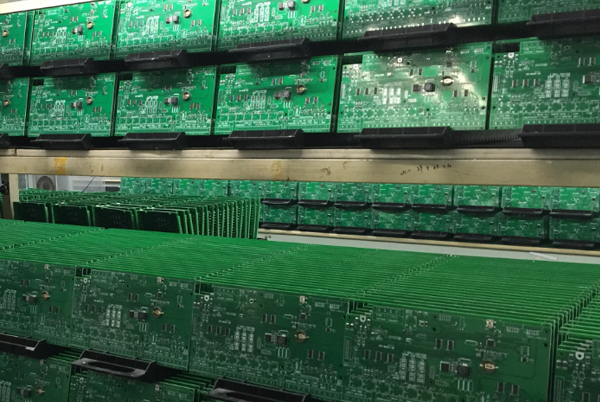
Evolução e contexto técnico da SMT
Contexto de desenvolvimento tecnológico
As tendências para a eletrónica inteligente, multimédia e em rede conduziram a três requisitos fundamentais para a tecnologia de montagem: alta densidade, alta velocidade e normalização. Estas exigências levaram à mudança revolucionária da tradicional tecnologia de orifícios (THT) para a tecnologia de montagem em superfície.
História do desenvolvimento global
A SMT teve origem na década de 1960 e passou por quatro fases principais:
- Exploração inicial (década de 1970): Utilizado principalmente em circuitos integrados híbridos e produtos de consumo, como relógios electrónicos e calculadoras
- Crescimento rápido (meados da década de 1980): Aumento da maturidade e expansão das aplicações
- Adoção generalizada (década de 1990): Tornou-se a principal tecnologia de montagem, substituindo gradualmente a THT
- Inovação contínua (século XXI - presente): Avançando para uma maior densidade, tamanho mais pequeno e melhor desempenho
Situação atual na China
A tecnologia SMT foi introduzida na China na década de 1980, inicialmente para a produção de sintonizadores de televisão, antes de se expandir para a eletrónica de consumo, como gravadores de vídeo e câmaras. Desde 2000, com o rápido desenvolvimento da indústria de informação eletrónica, as importações de equipamento SMT aumentaram substancialmente, estabelecendo a China como a maior base de produção SMT do mundo.
Principais vantagens da tecnologia SMT
- Montagem de alta densidade: Reduz o volume do produto em 60% e o peso em 75%
- Fiabilidade excecional: Taxas de defeitos nas juntas de soldadura inferiores em uma ordem de grandeza às do THT, com uma resistência superior ao choque
- Excelentes caraterísticas de alta frequência: Minimiza a capacitância e a indutância parasitas, reduzindo as interferências electromagnéticas
- Automatização eficiente: Simplifica os processos de produção e melhora a eficiência
- Vantagens significativas em termos de custos: Reduz os custos totais de produção em 30-50%
Principais tendências tecnológicas em SMT
Inovações na embalagem de componentes
A tecnologia de embalagem continua a evoluir para tamanhos mais pequenos, mais E/S e maior fiabilidade, com as principais tendências a incluírem:
- Integração do módulo multi-chip (MCM)
- Desenvolvimento de rede de resistências de chip
- Tecnologia System-in-Package (SiP)
- Integração de sistemas em chip (SoC)
- Aplicações Silicon-on-Insulator (SOI)
- Investigação de dispositivos nanoelectrónicos
Avanços no equipamento de produção
O equipamento SMT moderno está a progredir no sentido da eficiência, flexibilidade e sustentabilidade ambiental:
- Alta eficiência: A alimentação de placas de via dupla e os designs com várias cabeças aumentam a produtividade
- Sistemas Inteligentes: A inspeção por visão e os controlos digitais aumentam a precisão e a velocidade
- Configurações flexíveis: Os modelos modulares adaptam-se a diversas necessidades de produção
- Soluções ecológicas: Redução do ruído e controlo da poluição para uma produção ecológica
Inovações tecnológicas em placas de circuitos
Tendências de desenvolvimento das placas de montagem em superfície (SMB):
- Alta precisão: 0,06 mm de largura de linha, 0,08 mm de espaçamento
- Alta densidade: abertura mínima de 0,1 mm
- Desenhos ultra-finos: Placas de 6 camadas com 0,45-0,6 mm de espessura
- Construção de placas multicamadas: Interligações de alta densidade de 30-50 camadas
- Aumento das aplicações de placas flexíveis
- Utilização generalizada de substratos cerâmicos
- Tecnologias de revestimento de superfícies sem chumbo
Componentes principais dos processos SMT
Tipos de processos primários
- Refluxo de pasta de solda: Simples e eficiente para produtos miniaturizados
- Soldadura SMT-Wave: Combina componentes de montagem através de orifícios e de superfície
- Fluxo de pasta de solda de dupla face: Permite a montagem de densidade ultra-alta
- Montagem híbrida: Integra múltiplas vantagens tecnológicas
Principais processos da linha de produção
- Impressão de pasta de solda: Aplicação precisa nas placas de circuito impresso
- Colocação de componentes: Montagem de alta precisão de SMDs
- Soldadura por Refluxo: Cria ligações eléctricas fiáveis
- Limpeza e inspeção: Eliminação de resíduos e controlo de qualidade
Três pormenores críticos do processo
- Aplicação de pasta: Impressão automatizada ou semi-automatizada para uma distribuição homogénea
- Colocação de componentes: Posicionamento ao nível do mícron através de sistemas de colocação de precisão
- Soldadura por Refluxo: Perfil de temperatura preciso para uma soldadura óptima
Gestão da proteção contra descargas electrostáticas (ESD)
Riscos ESD
A eletricidade estática pode causar danos imediatos ou latentes nos componentes electrónicos, sendo os defeitos latentes responsáveis por 90% das falhas e representando ameaças significativas à qualidade.
Medidas de proteção
- Sistemas de proteção pessoal: Pulseiras, vestuário e calçado anti-estáticos
- Controlos ambientais: Pavimentos e superfícies de trabalho seguros em termos de ESD
- Protocolos operacionais: Procedimentos rigorosos de gestão ESD nas áreas de produção
Detalhes da tecnologia de processo SMT de três núcleos
1. Processo de aplicação de pasta de solda
Sendo o primeiro processo crítico nas linhas de produção SMT, a qualidade da aplicação da pasta de solda tem um impacto direto nas operações subsequentes. A impressão moderna de pasta de solda utiliza principalmente a tecnologia de impressão em estêncil, com aspectos técnicos fundamentais que incluem:
- Equipamento de impressão:
- As impressoras totalmente automáticas com sistemas de alinhamento de visão atingem uma precisão de posicionamento de ±12,5μm
- Os modelos semi-automáticos adequam-se à produção de lotes médios/pequenos
- Controlo de processos:
- O ângulo do rodo é normalmente mantido a 45-60°
- Velocidade de impressão controlada entre 20-80mm/s
- Pressão de impressão mantida entre 5 e 15 kg
- Desenho de estêncil:
- Seleção da espessura: 0,1-0,15 mm para componentes padrão, 0,08 mm para componentes de passo fino
- Desenho da abertura: O rácio de área >0,66 garante uma libertação adequada da pasta
- Gestão de pastas:
- Requer um recondicionamento mínimo de 4 horas antes da utilização
- 2-3 minutos de mistura para obter uma viscosidade óptima
- Condições ambientais: 23±3°C, 40-60% RH
2. Tecnologia de colocação de componentes
O núcleo do fabrico SMT, as máquinas de colocação modernas proporcionam uma montagem automatizada ultra-precisa:
- Tipos de equipamento:
- Colocadores de alta velocidade: Até 250.000 CPH para componentes pequenos
- Máquinas multi-funções: Manusear componentes de formas estranhas com uma precisão de ±25μm
- Sistemas modulares: Configurações flexíveis para diversas necessidades
- Parâmetros técnicos críticos:
- Precisão de colocação: ±30μm@3σ (as máquinas topo de gama atingem ±15μm)
- Tamanho mínimo do componente: 0201 (0,25×0,125 mm) ou mais pequeno
- Reconhecimento de componentes: CCD de alta resolução (até 0,01 mm/pixel)
- Controlos-chave do processo:
- Seleção e manutenção dos bicos
- Calibração do alimentador
- Controlo da força de colocação (10-500g ajustável)
- Calibração do sistema de alinhamento da visão
3. Processo de soldadura por refluxo
O processo crítico para juntas de solda fiáveis requer um controlo preciso da temperatura:
- Zonas de perfil de temperatura:
- Pré-aquecimento: Ambiente→150°C a uma taxa de rampa de 1-3°C/s
- Imersão: 150-180°C durante 60-90 segundos
- Refluxo: Temperatura de pico 220-245°C durante 30-60 segundos
- Arrefecimento: Taxa <4°C/s
- Tipos de equipamento:
- Refusão por convecção: Excelente uniformidade de temperatura
- Refusão por infravermelhos: Elevada eficiência térmica
- Sistemas híbridos: Combinar as duas vantagens
- Controlos críticos de processos:
- Teor de oxigénio (<1000ppm)
- Velocidade do tapete rolante (0,8-1,5 m/min)
- Colocação e monitorização de termopares
- Otimização do perfil para diferentes pastas
- Prevenção de defeitos comuns:
- Tombamento: Otimizar a conceção da almofada, controlar a taxa de rampa
- Ponte: Ajustar as aberturas do estêncil, parâmetros do rodo
- Juntas frias: Assegurar uma temperatura/duração de pico adequada
Estes três processos constituem o núcleo tecnológico do fabrico SMT. Cada um deles requer um controlo preciso do processo e uma gestão rigorosa da qualidade para garantir a fiabilidade e a consistência do produto final. As linhas modernas de SMT implementam sistemas MES para monitorização de dados de todo o processo, assegurando a rastreabilidade dos parâmetros e a estabilidade do processo.