Описание
A Ведомость материалов (BOM) это структурированный список, определяющий компоненты, детали, сырье и узлы, необходимые для производства продукта. Он служит основополагающим документом в производстве, подробно описывая иерархические отношения между родительскими и дочерними элементами, а также их количество.
Ключевые понятия:
-
Иерархическая структура: Представляет состав изделия от сборок верхнего уровня до отдельных деталей.
-
Многоотраслевое применение:
-
Дискретное производство: Показывает взаимосвязь механических и электронных компонентов (например, автомобильных, электронных).
-
Перерабатывающая промышленность: Указывает формулы с сырьем и соотношениями (например, химикаты, фармацевтические препараты).
-
Основной файл ERP/MRP: Критически важен для планирования материалов, расчета затрат и планирования производства.
Структура и типы BOM
1. Структурное представление
-
Одноуровневая спецификация: Перечисляет прямые компоненты родительского элемента.
-
Многоуровневая спецификация: Расширяется на подсборки (например, Product → Subassembly → Part).
-
Неразборная спецификация: Визуализирует иерархию с отступами (см. Рисунок 1).
2. Типы спецификаций по функциям
- тип |
Описание |
Пример использования |
Стандартная спецификация |
Определяет физические компоненты для производства. |
Производство смартфона. |
Планирование спецификации |
Использует процентные соотношения для прогнозирования семейств продуктов. |
Планирование спроса на модели автомобилей. |
Модель BOM |
Возможность конфигурирования с помощью дополнительных компонентов (ATO/PTO). |
Настраиваемые ноутбуки. |
Опция Класс BOM |
Группирует связанные опции в одну категорию. |
Пакеты автомобильной отделки. |
3. Комплектация на этапе разработки
-
Инженерная спецификация (EBOM): Ориентирован на проектирование, на основе систем CAD/PDM.
-
Технологическая спецификация (PBOM): Добавляет этапы производства и требования к оснастке.
-
Производственная спецификация (MBOM): Включает оперативные данные (маршруты, ресурсы).
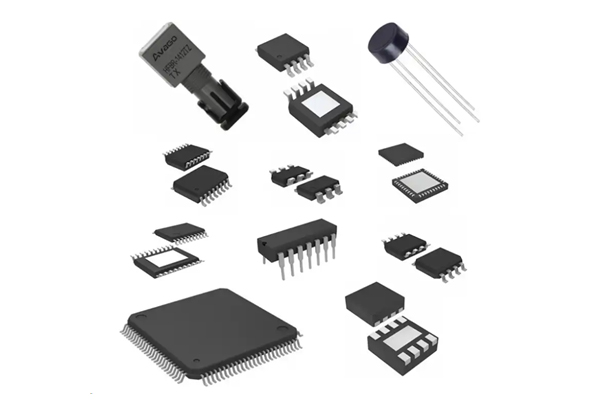
Основные функции и приложения
1. Межведомственное использование
-
Дизайн: Проверяет архитектуру продукта.
-
Производство: Руководит сборкой и выдачей материалов.
-
Закупки: Запускает заказы на поставку.
-
Расчет стоимости: Рассчитывает себестоимость продукции через сворачивание компонентов.
2. Интеграция ERP
-
Водитель MRP: Преобразование генерального графика производства (MPS) в требования к материалам.
-
Унифицированный источник данных: Связывает инженерное дело, планирование и финансы.
3. Расширенные форматы спецификаций
-
Матричная спецификация: Сравнивает варианты (например, семейства продуктов).
-
Модульная спецификация: Управляет конфигурируемыми изделиями (например, промышленным оборудованием).
Лучшие практики и проблемы
Критические факторы успеха
-
Точность: >98% точность, необходимая для эффективности ERP.
-
Контроль версий: Синхронизируйте переходы EBOM→MBOM.
-
Специальные компоненты: Ручка фантомы (товары, не находящиеся на складе) и наборы логически.
Распространенные подводные камни
-
Неправильное количество: Вызывает дефицит/избыток запасов.
-
Устаревшие предметы: Приводит к напрасному расходованию запасов.
-
Плохое обслуживание: Вызывает каскадные ошибки в MRP.
Методы валидации
-
Физические разрывы: Разборка изделий для проверки спецификаций.
-
Межфункциональные обзоры: Привлекать к работе инженерные, производственные и плановые группы.
-
Аналитика ERP: Отслеживайте незапланированные перемещения материалов (например, избыточные возвраты).
BOM в цифровой трансформации
1. Интеграция PDM/PLM
-
Автоматизируйте преобразование EBOM→MBOM с помощью правил рабочего процесса.
-
Встраивание производственных атрибутов (например, допусков, покрытий).
2. Приложения AI/ML
3. IoT и умное производство
Хорошо управляемая спецификация - основа эффективного производства, обеспечивающая бесперебойную координацию от разработки до поставки. Компании, инвестирующие в точность спецификаций и цифровую интеграцию, получают конкурентный контроль затрат, гибкость и преимущества при выводе продукции на рынок.