Flusso del processo di produzione dei PCB
Nel mondo di oggi, in cui i dispositivi elettronici sono onnipresenti, i PCB (Printed Circuit Boards) sono lo "scheletro" e il "sistema nervoso" dei prodotti elettronici e i loro processi di produzione hanno un impatto diretto sulle prestazioni e sull'affidabilità del prodotto. Che siate ingegneri elettronici, specialisti dell'approvvigionamento o semplicemente interessati alla produzione di PCB, la comprensione del flusso di lavoro completo di fabbricazione dei PCB è essenziale. Questo articolo vi illustrerà ogni fase critica della produzione di PCB, dalle materie prime al prodotto finito, affrontando le sfide più comuni della produzione.
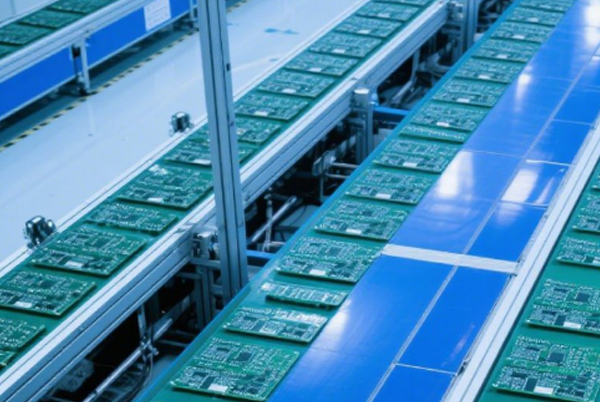
Indice per materie
Ripartizione dettagliata del nucleo Produzione PCB Processi
1. Taglio del pannello (CUT): Il punto di partenza della precisione
Il taglio dei pannelli rappresenta la prima fase della produzione di PCB e costituisce la base per i processi successivi. Pur essendo apparentemente semplice, comporta diverse considerazioni tecniche:
- Selezione materiale: I comuni materiali laminati rivestiti di rame includono FR-4 (fibra di vetro epossidica), substrati di alluminio e materiali ad alta frequenza (ad esempio, Rogers), ognuno dei quali richiede parametri di taglio diversi.
- Controllo dimensionale: Taglio preciso secondo le specifiche di progetto per le dimensioni di UNIT (circuito singolo), SET (array pannellati) e PANEL (pannello di produzione).
- Requisiti di precisione: La moderna produzione di PCB richiede in genere tolleranze di taglio entro ±0,10 mm.
- Trattamento dei bordi: I bordi tagliati devono essere sbavati per evitare che i bordi ruvidi influenzino i processi successivi.
Considerazioni chiave:
- Verificare il tipo di materiale, lo spessore e il peso del rame prima del taglio.
- Tenere conto dell'espansione/contrazione del materiale nei processi successivi quando si determinano le dimensioni del pannello.
- Mantenere un ambiente di lavoro pulito per evitare la contaminazione delle superfici.
- Conservare separatamente i diversi materiali per evitare che si mescolino
2. Imaging su film secco a strato interno: Creazione di schemi circuitali precisi
Il processo di film secco dello strato interno è fondamentale per trasferire con precisione i modelli di progetto sui substrati dei PCB e consiste in diversi sottoprocessi:
Preparazione della superficie (lavaggio dei pannelli)
- Combina la pulizia chimica con l'abrasione meccanica
- Rimuove l'ossidazione e crea micro-ruvidità per una migliore adesione del film secco
- Parametri tipici: Segni di sfregamento di 5-10 mm, rugosità Ra 0,3-0,5μm
Laminazione a secco
- Lega termicamente la pellicola fotosensibile secca alla superficie del rame
- Controllo della temperatura: Tipicamente 100-120°C
- Controllo della pressione: Circa 0,4-0,6MPa
- Controllo della velocità: 1,0-1,5 m/min
Esposizione
- Utilizza la luce UV (lunghezza d'onda di 365 nm) per polimerizzare selettivamente il film secco attraverso il fototool
- Controllo dell'energia: 5-10mJ/cm²
- Precisione di registrazione: Entro ±25μm
Sviluppo
- Utilizza la soluzione di carbonato di sodio 1% per sciogliere il film secco non polimerizzato.
- Controllo della temperatura: 28-32°C
- Pressione di spruzzo: 1,5 - 2,5 bar
Incisione
- Utilizza una soluzione acida di cloruro di rame (CuCl2+HCl) per dissolvere il rame esposto.
- Fattore di mordenzatura (controllo dell'incisione laterale) >3,0
- Uniformità dello spessore del rame entro ±10%
Striscia
- Utilizza una soluzione di idrossido di sodio 3-5% per rimuovere la pellicola protettiva secca.
- Controllo della temperatura: 45-55°C
- Controllo del tempo: 60-90 secondi
Progettazione raccomandata:
- Traccia/spazio minimo dello strato interno ≥ 3 mil (0,075 mm)
- Evitare elementi di rame isolati per evitare l'incisione eccessiva.
- Distribuire uniformemente il rame per evitare la deformazione della laminazione
- Aggiungere margine di progettazione per le tracce di segnali critici
3. Trattamento con ossido bruno: Miglioramento del legame tra gli strati
Il trattamento con ossido bruno è fondamentale per la produzione di PCB multistrato, soprattutto per migliorare l'adesione tra lo strato interno di rame e il preimpregnato (PP):
- Reazione chimica: Forma uno strato complesso organico-metallico micro-ruvido sulla superficie del rame.
- Controllo del processo:
- Temperatura: 30-40°C
- Tempo: 1,5-3 minuti
- Aumento dello spessore del rame: 0,3-0,8μm
- Verifica della qualità:
- Uniformità del colore
- Test dell'angolo di contatto con l'acqua (dovrebbe essere ≥30°)
- Prova di resistenza alla pelatura (≥1,0N/mm)
Problemi comuni:
- Un trattamento insufficiente può causare delaminazione dopo la laminazione
- L'eccessivo trattamento crea una rugosità eccessiva che compromette l'integrità del segnale.
- I pannelli lavorati devono essere laminati entro 8 ore.
4. Laminazione: Formazione di strutture multistrato
La laminazione unisce più anime di strati interni con il preimpregnato (PP) sotto calore e pressione per creare strutture multistrato:
- Preparazione materiale:
- Foglio di rame (in genere 1/3 oz o 1/2 oz)
- Preimpregnati (ad esempio, gradi 1080, 2116, 7628)
- Piastre in acciaio inox, carta kraft e altri materiali ausiliari
- Parametri di processo:
- Temperatura: 170-190°C
- Pressione: 15-25 kg/cm²
- Tempo: 90-180 minuti (a seconda dello spessore e della struttura della tavola)
- Controlli critici:
- Velocità di riscaldamento: 2-3°C/min
- Velocità di raffreddamento: 1-2°C/min
- Livello di vuoto: ≤100mbar
Considerazioni sulla progettazione:
- Mantenere l'impilamento simmetrico (ad esempio, scheda a 8 strati: 1-2-3-4-4-3-2-1)
- Orientare le tracce dei livelli adiacenti in modo perpendicolare (ad esempio, orizzontale su un livello, verticale su quello adiacente).
- Utilizzare PP ad alto contenuto di resina per i pannelli di rame pesanti
- Considerare il flusso del materiale durante la laminazione per i progetti con passaggio cieco/interrotto
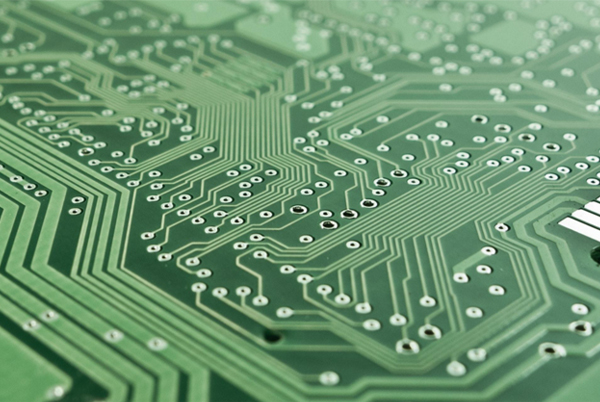
5. Foratura: Creare interconnessioni di precisione
La foratura crea interconnessioni verticali tra gli strati del circuito stampato, con una tecnologia moderna che consente di ottenere una precisione eccezionale:
- Tipi di trapano:
- Foratura meccanica (per fori ≥0,15 mm)
- Foratura laser (per microvias e blind vias)
- Parametri tipici:
- Velocità del mandrino: 80.000-150.000 giri/min.
- Velocità di avanzamento: 1,5-4,0 m/min
- Velocità di rientro: 10-20m/min
- Norme di qualità:
- Rugosità della parete del foro ≤25μm
- Precisione della posizione del foro ±0,05 mm
- Nessun chiodo o sbavatura
Risoluzione dei problemi comuni:
- Pareti a fori grezzi: Ottimizzare i parametri di perforazione, utilizzare materiali di ingresso/backup adeguati.
- Fori intasati: Migliorare l'evacuazione dei trucioli, regolare la sequenza di foratura
- Trapani rotti: Verifica della qualità della perforazione, ottimizzazione delle velocità di avanzamento
6. Deposizione di rame chimico (PTH): Metallizzazione a foro critico
La deposizione di rame elettrolitico crea strati conduttivi sulle pareti dei fori non conduttivi, fondamentali per l'affidabilità dei PCB:
Flusso del processo PTH
- Dissolvenza: Rimuove i residui di resina dalla perforazione
- Rame elettrolitico:
- Una soluzione alcalina che utilizza la formaldeide come agente riducente
- Temperatura: 25-32°C
- Tempo: 15-25 minuti
- Spessore del rame: 0,3-0,8μm
- Placcatura del pannello:
- Soluzione acida di solfato di rame
- Densità di corrente: 1,5-2,5ASD
- Tempo: 30-45 minuti
- Spessore del rame: 5-8μm
Requisiti di qualità:
- Test della retroilluminazione ≥9 livello (≥90% copertura della parete del foro)
- Test di stress termico (288°C, 10 secondi) senza delaminazione o formazione di bolle.
- Resistenza di foro ≤300μΩ/cm
7. Trasferimento del modello dello strato esterno
Simile all'imaging dello strato interno, ma con fasi di placcatura aggiuntive:
- Preparazione della superficie: Pulizia, micro-etch (rimuove 0,5-1μm di rame)
- Laminazione a secco: Utilizza un film secco resistente alla placcatura
- Esposizione: Utilizza l'LDI (Laser Direct Imaging) o un fototool tradizionale.
- Sviluppo: Crea un modello di placcatura
- Placcatura del modello:
- Spessore del rame: 20-25μm (totale)
- Spessore dello stagno: 3-5μm (come etch resist)
- Striscia: Rimuove la resistenza alla placcatura
- Incisione: Rimuove il rame indesiderato
Punti salienti della tecnica:
- Compensazione della larghezza della traccia: Regola la larghezza del progetto in base allo spessore del rame (in genere aggiunge 10-20%)
- Uniformità di placcatura: Utilizzare una soluzione ad alta potenza di lancio e una configurazione anodica adeguata.
- Controllo dell'incisione laterale: Ottimizzazione dei parametri di incisione per mantenere l'accuratezza della larghezza della traccia
8. Maschera di saldatura: Strato di protezione del circuito
La maschera di saldatura protegge i circuiti e influisce sulla qualità e sull'aspetto della saldatura:
- Metodi di applicazione:
- Stampa serigrafica: Per requisiti di bassa precisione
- Rivestimento a spruzzo: Per forme irregolari dei pannelli
- Rivestimento a tenda: Alta efficienza, eccellente uniformità
- Flusso di processo:
- Preparazione della superficie (pulizia, irruvidimento)
- Applicazione della maschera di saldatura
- Pre-cottura (75°C, 20-30 minuti)
- Esposizione (300-500mJ/cm²)
- Sviluppo (soluzione di carbonato di sodio 1%)
- Polimerizzazione finale (150°C, 30-60 minuti)
- Norme di qualità:
- Durezza ≥6H (durezza della matita)
- Adesione: 100% supera il test del nastro adesivo 3M.
- Resistenza alla saldatura: 288°C, 10 secondi, 3 cicli senza difetti
Linee guida per la progettazione:
- Ponte minimo della maschera di saldatura ≥0,1 mm
- Aperture dell'area BGA: 0,05 mm più grandi delle piazzole per lato
- Le dita dorate richiedono la copertura della maschera di saldatura
9. Finitura superficiale: bilanciamento tra saldabilità e durata
Finiture diverse si adattano a diverse applicazioni:
Tipo di finitura | Gamma di spessore | vantaggi | Svantaggi | Applicazioni tipiche |
---|---|---|---|---|
HASL | 1-25μm | Basso costo, eccellente saldabilità | Scarsa planarità, non per il passo fine | Elettronica di consumo |
ENIG | Ni3-5μm/Au0,05-0,1μm | Eccellente planarità, lunga durata di conservazione | Costo elevato, rischio di black pad | Prodotti ad alta affidabilità |
OSP | 0,2-0,5μm | Basso costo, processo semplice | Breve durata di conservazione (6 mesi) | Elettronica di consumo ad alto volume |
Imm Ag | 0,1-0,3μm | Buona saldabilità, costo moderato | Incline all'appannamento, è necessario un imballaggio speciale | Circuiti RF/alta frequenza |
ENEPIG | Ni3-5μm/Pd0.05-0.1μm/Au0.03-0.05μm | Compatibile con diversi metodi di assemblaggio | Costo più alto | Imballaggio avanzato |
Guida alla selezione:
- Elettronica di consumo standard: HASL o OSP
- Prodotti ad alta affidabilità: ENIG
- Circuiti ad alta velocità: Imm Ag o OSP
- Connettori di bordo: Placcatura in oro duro (1-3μm)
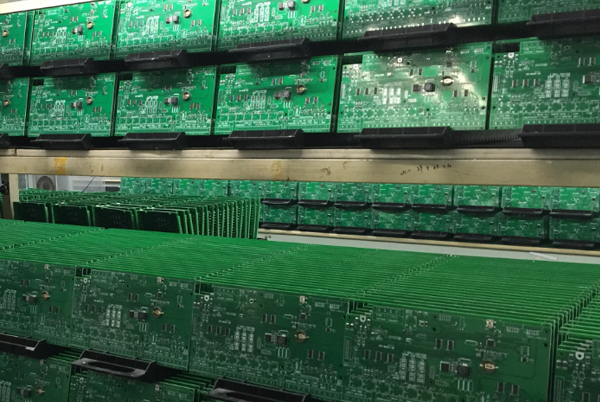
10. Fresatura: Realizzazione di contorni di precisione
L'elaborazione dei contorni dei PCB utilizza principalmente tre metodi:
- Fresatura CNC:
- Precisione: ±0,10 mm
- Larghezza minima della fessura: 1,0 mm
- Raggio d'angolo: ≥0,5 mm
- Punteggio a V:
- Angolo: 30° o 45°
- Spessore rimanente: 1/3 dello spessore della tavola (in genere 0,3-0,5 mm)
- Precisione di posizione: ±0,10 mm
- Taglio laser:
- Precisione: ±0,05 mm
- Taglio minimo: 0,2 mm
- Nessuna sollecitazione meccanica
Regole di progettazione:
- Mantenere uno spazio di ≥0,3 mm tra il bordo della scheda e i circuiti.
- Includono linguette a strappo o mouse bites per i progetti a pannelli.
- Fornite file DXF precisi per contorni irregolari
- Bordi smussati (in genere 20-45°) per le tavole con dita dorate
11. Test elettrico: Cancello finale della qualità
Il collaudo dei circuiti stampati garantisce l'affidabilità funzionale:
- Metodi di prova:
- Sonda volante: Adatta per la produzione di bassi volumi e alte miscele
- Test dei dispositivi: Per la produzione di grandi volumi
- AOI (Ispezione ottica automatizzata): Ispezione supplementare
- Copertura del test:
- 100% continuità netta
- Test di isolamento (tipicamente 500 V CC)
- Test di impedenza (per schede a impedenza controllata)
Risoluzione di problemi comuni:
- Aperture: Verificare le false aperture (contatto difettoso della sonda di prova)
- Corti: Analizzare la posizione dei corti, verificare i problemi di progettazione
- Deviazione dell'impedenza: Verificare i parametri del materiale e il controllo della larghezza della traccia
12. Ispezione finale e imballaggio
L'ultima fase di verifica della qualità:
- Elementi di ispezione:
- Visivo: graffi, macchie, difetti della maschera di saldatura
- Dimensioni: Spessore, profilo, dimensioni dei fori
- Marcatura: Chiarezza della legenda e precisione della posizione
- Funzionale: Qualità della placcatura a dito d'oro, test di impedenza
- Metodi di imballaggio:
- Confezionamento sottovuoto (antiossidazione)
- Imballaggio antistatico (per componenti sensibili)
- Carta interfogliata (evita i graffi superficiali)
- Vassoi personalizzati (per schede di alta precisione)
Standard di spedizione:
- IPC-A-600G Classe 2 (commerciale)
- IPC-A-600G Classe 3 (alta affidabilità)
- Requisiti specifici del cliente
Domande e risposte sulla produzione di PCB
D1: Perché il mio PCB presenta un distacco di rame dopo la saldatura?
Cause principali:
- Scarsa adesione del rame al substrato (problema del materiale)
- Temperatura o durata di saldatura eccessiva
- Progettazione inadeguata (ad esempio, un'ampia area di rame collegata tramite tracce sottili)
- Trattamento inadeguato dell'ossido bruno
Soluzioni:
- Selezionare materiali laminati di alta qualità
- Ottimizzazione dei parametri di saldatura (<260°C, <5 secondi)
- Utilizzare connessioni di scarico termico nelle progettazioni
- Verificare i parametri del processo di ossido bruno con il produttore.
- Eseguire test di stress termico quando necessario (288°C, 10 secondi, 3 cicli).
D2: Come affrontare la disregistrazione da strato a strato nei PCB multistrato?
Fonti di registrazione errata:
- Incoerenze di espansione/contrazione dei materiali
- Spostamento dello strato durante la laminazione
- Precisione di registrazione dell'esposizione insufficiente
- Deviazioni della posizione di perforazione
Misure di miglioramento:
- Fase di progettazione:
- Aggiungere obiettivi di registrazione (minimo 3)
- Mantenere una distribuzione uniforme del rame
- Tenere conto delle proprietà del materiale (gestione speciale per i materiali ad alta frequenza)
- Produzione:
- Utilizzare apparecchiature di esposizione LDI ad alta precisione
- Implementare l'allineamento della perforazione a raggi X
- Applicare algoritmi di compensazione del ritiro del materiale
- Considerare la laminazione sequenziale per i pannelli ad alto rapporto d'aspetto
- Selezione del materiale:
- Utilizzare materiali a basso CTE
- Selezionare un preimpregnato dimensionalmente stabile
D3: Come risolvere le pareti ruvide dei fori piccoli (<0,2 mm)?
Soluzioni tecniche:
- Selezione della trivella:
- Esercitazioni speciali (ad esempio, di tipo UC)
- Angolo del punto 130-140°
- Angolo elica 35-40°
- Ottimizzazione dei parametri:
- Aumentare il numero di giri a 120.000-150.000
- Ridurre la velocità di avanzamento a 1,0-1,5 m/min.
- Cambiare le esercitazioni ogni 500 colpi
- Materiali ausiliari:
- Materiale d'ingresso in alluminio ad alta densità
- Pannelli di supporto speciali (ad esempio, fenolici)
- Post-elaborazione:
- Desmear potenziato (trattamento al plasma opzionale)
- Ottimizzare l'etchback prima del rame elettrolitico
D4: Come devono essere progettate le aperture della maschera di saldatura per le aree BGA?
Specifiche di progettazione:
- BGA standard:
- Aperture della maschera di saldatura di 0,05 mm più grandi delle piazzole per lato
- Ponte minimo della maschera di saldatura 0,1 mm
- Design NSMD (Non-Solder Mask Defined)
- BGA a passo fine (passo ≤0,5 mm):
- Aperture della maschera di saldatura uguali o leggermente più piccole (0,02-0,03 mm) delle piazzole
- Progettazione SMD (Solder Mask Defined)
- Considerate il processo LDI (Laser Direct Imaging)
- Trattamenti speciali:
- Impedire alla maschera di saldatura di arrampicarsi sulle sfere BGA
- Controllo dello spessore della maschera di saldatura a 10-15μm
- Implementare le dighe per le maschere di saldatura quando necessario
Risoluzione di problemi comuni:
- La maschera di saldatura spessa causa problemi di saldatura: Utilizzare inchiostri per maschere di saldatura sottili
- Ponti di maschera di saldatura rotti: Ottimizzare l'energia di esposizione e lo sviluppo
- Aperture disallineate: Verificare i dati del fototool o dell'LDI
D5: Perché la placcatura ENIG a volte si trasforma in "Black Pad"? Come prevenirlo?
Cause del tampone nero:
Black Pad si riferisce alle interfacce fragili tra nichel e saldatura nelle finiture ENIG, causate principalmente da:
- Sovrametallizzazione del nichel durante la deposizione dell'oro
- Contenuto anomalo di nichel fosforo (dovrebbe essere 7-9%)
- Spessore eccessivo dell'oro (>0,15μm) che causa la passivazione del nichel
- Post-trattamento improprio (pulizia inadeguata)
Metodi di prevenzione:
- Controllo dei processi:
- Mantenere il pH del bagno a 4,5-5,5
- Spessore dell'oro di controllo 0,05-0,10μm
- Aggiungere un trattamento successivo all'immersione (ad esempio, un lavaggio con acido leggero).
- Monitoraggio della qualità:
- Analisi periodica del contenuto di nichel e fosforo
- Analisi della sezione trasversale dell'interfaccia nichel-oro
- Test di taglio delle sfere saldate (>5kg/mm²)
- Soluzioni alternative:
- Considerare ENEPIG (oro per immersione in nichel palladio senza metalli)
- Utilizzare nichel/oro elettrolitico per applicazioni ad alta affidabilità
D6: Come affrontare i problemi di integrità del segnale nei PCB ad alta velocità?
Co-ottimizzazione della progettazione e della produzione:
- Selezione materiale:
- Materiali a bassa Dk (costante dielettrica), bassa Df (fattore di dissipazione)
- Fogli di rame lisci (ad es., HVLP)
- Ottimizzazione del design:
- Controllo stretto dell'impedenza (±10%)
- Ridurre al minimo gli stub (foratura posteriore)
- Utilizzare strutture a microstriscia o stripline
- Controlli di produzione:
- Precisione di mordenzatura (larghezza traccia ±15μm)
- Controllo dello spessore del dielettrico (±10%)
- Selezione della finitura superficiale (preferibile Imm Ag o OSP)
- Test di verifica:
- Test TDR (Riflettometria nel dominio del tempo)
- Misure di perdita di inserzione/ritorno
- Test del diagramma a occhio (per segnali ad alta velocità)
Parametri tipici:
- segnali a 10 Gbps: Materiali con Df<0,010
- 28Gbps+: Considerare i materiali Megtron6 o Rogers
- Impedenza: 50Ω single-ended, 100Ω differenziale (regolare per protocollo)
conclusioni
La produzione di PCB rappresenta una tecnologia multidisciplinare che combina scienza dei materiali, processi chimici e ingegneria meccanica di precisione. Con l'evoluzione dell'elettronica verso frequenze, velocità e densità più elevate, i processi di fabbricazione dei PCB continuano a progredire di conseguenza. La comprensione di questi flussi di lavoro non solo facilita la progettazione di PCB più producibili, ma consente anche una rapida risoluzione dei problemi e una comunicazione efficace con i produttori.
Che si tratti di materiali FR-4 convenzionali per l'elettronica di consumo, di materiali specializzati ad alta frequenza per le apparecchiature 5G o di elettronica automobilistica ad alta affidabilità, la scelta dei produttori di PCB appropriati e la comprensione approfondita delle loro capacità si rivelano fondamentali. Ci auguriamo che questa guida fornisca spunti preziosi per supportare le vostre decisioni informate sulla produzione di PCB.
Messaggi correlati