La tecnologia SMT (Surface Mount Technology) rappresenta il cuore dell'assemblaggio elettronico moderno, trasformando i tradizionali componenti discreti a foro passante in dispositivi compatti senza piombo o con chip a piombo corto montati direttamente sulle superfici dei circuiti stampati. Questa tecnologia consente di assemblare prodotti elettronici ad alta densità, altamente affidabili, miniaturizzati ed economici, supportando al contempo processi di produzione automatizzati.
Panoramica della tecnologia di montaggio superficiale
La tecnologia a montaggio superficiale (SMT) ha rivoluzionato la produzione elettronica moderna, sostituendo gli ingombranti componenti a foro passante con dispositivi compatti a chip senza piombo che si montano direttamente sui circuiti stampati. Come processo di assemblaggio dominante nel settore, la SMT consente la produzione automatizzata di dispositivi elettronici ad alta densità, ultra-affidabili e miniaturizzati a costi ridotti. Questa tecnologia trasformativa è diventata onnipresente nei sistemi informatici, nelle apparecchiature di comunicazione e in innumerevoli prodotti elettronici, e la sua adozione continua ad espandersi con il declino dell'uso dei componenti tradizionali a foro passante. Il continuo progresso dei processi e dei componenti SMT l'ha resa un punto di riferimento per l'assemblaggio dei componenti elettronici, favorendo l'innovazione e soddisfacendo la crescente domanda di dispositivi elettronici più piccoli, più potenti e più efficienti in termini di costi in tutti i settori di mercato.
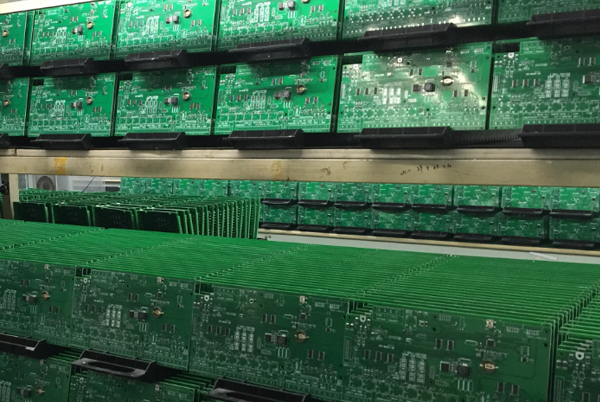
Evoluzione e contesto tecnico dell'SMT
Contesto di sviluppo tecnologico
Le tendenze verso un'elettronica intelligente, multimediale e in rete hanno determinato tre requisiti fondamentali per la tecnologia di assemblaggio: alta densità, alta velocità e standardizzazione. Queste esigenze hanno determinato il passaggio rivoluzionario dalla tradizionale tecnologia a fori passanti (THT) alla tecnologia a montaggio superficiale.
Storia dello sviluppo globale
L'SMT è nato negli anni '60 e ha attraversato quattro fasi fondamentali:
- Esplorazione iniziale (anni '70): Utilizzato principalmente nei circuiti integrati ibridi e nei prodotti di consumo come orologi e calcolatrici elettroniche.
- Crescita rapida (metà anni '80): Maturità crescente e applicazioni ampliate
- Adozione diffusa (anni '90): È diventata una tecnologia di assemblaggio mainstream, sostituendo gradualmente il THT.
- Innovazione continua (21° secolo-oggi): Progressi verso una maggiore densità, dimensioni ridotte e migliori prestazioni
Stato attuale in Cina
La tecnologia SMT è stata introdotta in Cina negli anni '80, inizialmente per la produzione di sintonizzatori televisivi, prima di espandersi all'elettronica di consumo, come videoregistratori e fotocamere. Dal 2000, con il rapido sviluppo dell'industria dell'informazione elettronica, le importazioni di apparecchiature SMT sono cresciute notevolmente, facendo della Cina la più grande base produttiva SMT del mondo.
I principali vantaggi della tecnologia SMT
- Assemblaggio ad alta densità: Riduce il volume del prodotto di 60% e il peso di 75%.
- Affidabilità eccezionale: Tassi di difettosità dei giunti a saldare inferiori di un ordine di grandezza rispetto al THT, con una resistenza superiore agli urti
- Eccellenti caratteristiche ad alta frequenza: Riduce al minimo la capacità e l'induttanza parassite, riducendo le interferenze elettromagnetiche.
- Automazione efficiente: Semplifica i processi produttivi e migliora l'efficienza
- Vantaggi significativi in termini di costi: Riduce i costi di produzione totali del 30-50%
Tendenze tecnologiche chiave nel settore SMT
Innovazioni nell'imballaggio dei componenti
La tecnologia del packaging continua a evolversi verso dimensioni più ridotte, un maggior numero di I/O e una maggiore affidabilità, con tendenze importanti quali:
- Integrazione del modulo multichip (MCM)
- Sviluppo della rete di resistenze su chip
- Tecnologia System-in-Package (SiP)
- Integrazione di sistemi su chip (SoC)
- Applicazioni in silicio su isolatore (SOI)
- Ricerca sui dispositivi nanoelettronici
Progressi delle apparecchiature di produzione
Le moderne apparecchiature SMT stanno progredendo verso l'efficienza, la flessibilità e la sostenibilità ambientale:
- Alta efficienza: L'alimentazione delle schede a doppia corsia e i design a più teste aumentano la produttività
- Sistemi intelligenti: L'ispezione visiva e i controlli digitali migliorano la precisione e la velocità
- Configurazioni flessibili: I design modulari soddisfano le diverse esigenze di produzione
- Soluzioni eco-compatibili: Riduzione del rumore e controllo dell'inquinamento per una produzione ecologica
Innovazioni nella tecnologia dei circuiti stampati
Tendenze di sviluppo delle schede a montaggio superficiale (SMB):
- Alta precisione: 0,06 mm di larghezza di linea, 0,08 mm di spaziatura
- Alta densità: apertura minima di 0,1 mm
- Progetti ultrasottili: Schede a 6 strati con spessore di 0,45-0,6 mm
- Realizzazione di schede multistrato: interconnessioni ad alta densità a 30-50 strati
- Aumento delle applicazioni dei pannelli flessibili
- Uso diffuso di substrati ceramici
- Tecnologie di rivestimento superficiale senza piombo
Componenti fondamentali dei processi SMT
Tipi di processo primario
- Pasta saldante a riflusso: Semplice ed efficiente per prodotti miniaturizzati
- Saldatura SMT-Wave: Combina componenti a foro passante e a montaggio superficiale
- Pasta saldante a riflusso su entrambi i lati: Consente l'assemblaggio ad altissima densità
- Assemblaggio ibrido: Integra molteplici vantaggi tecnologici
Processi chiave della linea di produzione
- Stampa della pasta saldante: Applicazione precisa alle piazzole dei circuiti stampati
- Posizionamento dei componenti: Montaggio di SMD ad alta precisione
- Saldatura a riflusso: Crea connessioni elettriche affidabili
- Pulizia e ispezione: Rimuove i residui e verifica la qualità
Tre dettagli critici del processo
- Applicazione della pasta: Stampa automatizzata o semi-automatizzata per una distribuzione uniforme
- Posizionamento dei componenti: Posizionamento a livello di micron tramite sistemi di posizionamento di precisione
- Saldatura a riflusso: Profilazione precisa della temperatura per una saldatura ottimale
Gestione della protezione dalle scariche elettrostatiche (ESD)
Rischi ESD
L'elettricità statica può causare danni immediati o latenti ai componenti elettronici; i difetti latenti sono responsabili della 90% maggior parte dei guasti e rappresentano una minaccia significativa per la qualità.
Misure di protezione
- Sistemi di protezione personale: Cinghie da polso, indumenti e calzature antistatiche
- Controlli ambientali: Pavimenti e superfici di lavoro a prova di ESD
- Protocolli operativi: Procedure di gestione ESD rigorose nelle aree di produzione
Dettagli sulla tecnologia di processo SMT a tre anime
1. Processo di applicazione della pasta saldante
Essendo il primo processo critico nelle linee di produzione SMT, la qualità dell'applicazione della pasta saldante influisce direttamente sulle operazioni successive. La moderna stampa della pasta saldante utilizza principalmente la tecnologia di stampa a stencil, con aspetti tecnici chiave quali:
- Apparecchiature di stampa:
- Le stampanti completamente automatiche con sistemi di allineamento visivo raggiungono una precisione di posizionamento di ±12,5μm
- I modelli semiautomatici sono adatti alla produzione di lotti medio/piccoli
- Controllo del processo:
- L'angolo del tergipavimento è tipicamente mantenuto a 45-60°.
- Velocità di stampa controllata tra 20-80 mm/s
- Pressione di stampa mantenuta a 5-15 kg
- Design dello stencil:
- Selezione dello spessore: 0,1-0,15 mm per i componenti standard, 0,08 mm per i componenti a passo fine
- Design dell'apertura: Il rapporto d'area >0,66 garantisce un corretto rilascio della pasta.
- Gestione della pasta:
- Richiede un ricondizionamento di almeno 4 ore prima dell'uso
- 2-3 minuti di miscelazione per ottenere una viscosità ottimale
- Condizioni ambientali: 23±3°C, 40-60% RH
2. Tecnologia di posizionamento dei componenti
Il cuore della produzione SMT, le moderne macchine di posizionamento consentono un assemblaggio automatizzato ultra-preciso:
- Tipi di apparecchiature:
- Placcatrici ad alta velocità: Fino a 250.000 CPH per piccoli componenti
- Macchine multifunzione: Manipolazione di componenti di forma strana con una precisione di ±25μm
- Sistemi modulari: Configurazioni flessibili per esigenze diverse
- Parametri tecnici critici:
- Precisione di posizionamento: ±30μm@3σ (le macchine di fascia alta raggiungono ±15μm)
- Dimensione minima del componente: 0201 (0,25×0,125 mm) o inferiore
- Riconoscimento dei componenti: CCD ad alta risoluzione (fino a 0,01 mm/pixel)
- Controlli chiave di processo:
- Selezione e manutenzione degli ugelli
- Calibrazione dell'alimentatore
- Controllo della forza di posizionamento (regolabile da 10 a 500 g)
- Calibrazione del sistema di allineamento di visione
3. Processo di saldatura a riflusso
Il processo critico per ottenere giunti di saldatura affidabili richiede un controllo preciso della temperatura:
- Zone del profilo di temperatura:
- Preriscaldamento: Ambiente→150°C con velocità di rampa di 1-3°C/s
- Ammollo: 150-180°C per 60-90 secondi
- Riflusso: Temperatura di picco 220-245°C per 30-60 secondi
- Raffreddamento: Velocità <4°C/s
- Tipi di apparecchiature:
- Riflusso a convezione: Eccellente uniformità di temperatura
- Riflusso a infrarossi: Alta efficienza termica
- Sistemi ibridi: Combinare entrambi i vantaggi
- Controlli di processo critici:
- Contenuto di ossigeno (<1000ppm)
- Velocità del trasportatore (0,8-1,5 m/min)
- Posizionamento e monitoraggio delle termocoppie
- Ottimizzazione del profilo per diverse paste
- Prevenzione dei difetti comuni:
- Tombstoning: Ottimizzare il design del pad, controllare la velocità di rampa
- Ponti: Regolare le aperture della matrice, i parametri della racla.
- Giunti a freddo: Assicurare una temperatura/durata di picco adeguata
Questi tre processi costituiscono il cuore tecnologico della produzione SMT. Ognuno di essi richiede un controllo preciso del processo e una gestione rigorosa della qualità per garantire l'affidabilità e la coerenza del prodotto finale. Le moderne linee SMT implementano sistemi MES per il monitoraggio completo dei dati di processo, garantendo la tracciabilità dei parametri e la stabilità del processo.