Descrição
Na indústria aeroespacial, a escolha de materiais e componentes para placas de circuito impresso (PCBA) não é uma questão de sorte. Imagine que estes dispositivos electrónicos têm de passar pelo lançamento de um foguetão com vibrações severas, mudanças extremas de temperatura no espaço e um ambiente de forte radiação; os materiais comuns simplesmente não conseguem suportar esta "tortura".
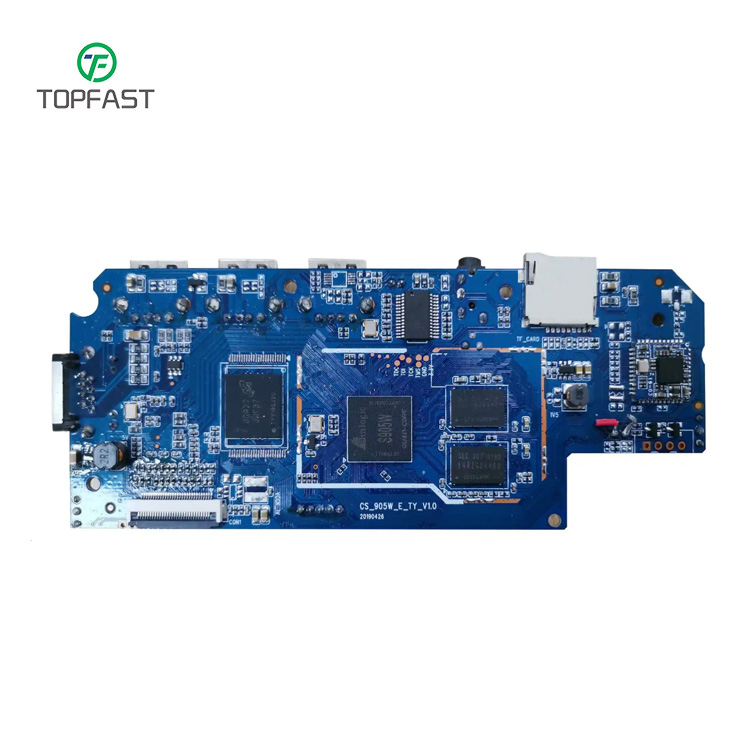
Diretrizes básicas para PCBA
1. substrato de PCB
O substrato das placas de circuitos aeroespaciais deve cumprir as quatro normas diamantadas:
Resistência a altas temperaturas: para resistir ao frio extremo e ao calor de torturas repetidas
Resistência à corrosão: todos os tipos de radiação e produtos químicos no espaço não podem prejudicá-lo nem um pouco
Bom isolamento: a transmissão do sinal deve ser estável e fiável
Robusto e durável: não pode ser quebrado mesmo com a vibração violenta durante o lançamento.
Os materiais de "qualidade espacial" comummente utilizados incluem:
Poliimida (PI): como um "colete à prova de bala" para placas de circuitos, é particularmente resistente a altas temperaturas.
Cianoacrilato (CE): um produto equilibrado com "desempenho superior".
Substrato cerâmico: desempenho de dissipação de calor de primeira classe do "especialista em arrefecimento".
2. seleção de componentes
1. chip (IC) como escolher?
Reconhecer a certificação: A certificação QML-V/QML-Q é a "autorização de trabalho".
Conceção anti-radiação: os raios cósmicos devem ter a "máscara do sino de ouro".
Não procurem o mais recente, mas sim o mais estável: O processo de 65 nm ou mais maduro é mais fiável
2. Componentes passivos
Condensadores: Os condensadores de tântalo são a força principal, os condensadores de cerâmica devem ser do tipo COG/NPO.
Resistências: as resistências de película são a primeira escolha, as resistências de folha metálica têm o melhor desempenho.
Indutores: os indutores com núcleo de ferrite ou com núcleo de ar são os mais fiáveis.
3. Conectores
Norma: MIL-DTL-38999/32139 é o requisito básico.
Revestimento de ouro: Os contactos devem ser revestidos com, pelo menos, 50 micropolegadas de ouro.
Seguro duplo: deve estar equipado com um mecanismo de bloqueio secundário
3. processos especiais
Tecnologia de encapsulamento
A embalagem de cerâmica é a primeira escolha, como um "fato espacial" para o chip.
As embalagens de plástico devem ser certificadas pelo exército
As embalagens BGA não devem ser utilizadas, exceto se forem especialmente reforçadas
Soldadura
A solda tradicional com alto teor de Pb (Sn63Pb37) ainda é dominante
Se for utilizado um processo sem chumbo, é necessária uma verificação adicional
Exame de raio X após a soldadura para garantir que não existem "lesões internas".
Tratamentos de proteção
Os revestimentos devem cumprir a norma militar MIL-I-46058.
Os revestimentos de parileno são mais eficazes
A espessura do revestimento deve ser controlada dentro do intervalo da espessura de um cabelo.
4. gestão da cadeia de abastecimento
Canal de compras
Só adquirir produtos da fábrica original ou de distribuidores autorizados
Resistir à contrafação de componentes
Cada componente deve ter um "cartão de identificação", para que todo o processo possa ser rastreado.
Inspeção da qualidade
100% inspeção dos materiais recebidos, ninguém pode ser deixado de fora
Ensaios aleatórios de desmontagem, não inferiores a 10%.
Ensaio de envelhecimento acelerado para prever a vida útil
Gestão da mudança
Qualquer alteração deve ser novamente verificada
A mudança de componentes equivale a uma nova certificação
Todos os registos de alterações devem ser mantidos na íntegra

Aeroespacial PCBA processo de soldadura
1. processo de soldadura
No sector aeroespacial, uma junta de soldadura não qualificada pode ser o "calcanhar de Aquiles" de toda a missão. Uma vez que o equipamento tem de ser submetido a repetidas "torturas", desde o frio extremo ao calor extremo, o processo de soldadura tem de ser infalível.
1. Processo de soldadura: três grandes diamantes
Soldadura por onda: adequada para soldadura de alto volume de componentes através de orifícios, como uma montanha-russa, com a PCB a passar através da solda fundida
Soldadura por refluxo (opção principal): tecnologia precisa de "aquecimento local", especialmente adequada para componentes de circuitos integrados
Soldadura por onda selectiva: Tecnologia de "soldadura por pontos de precisão" para juntas de soldadura específicas.
2. Processo de refluxo
Os perfis de temperatura são fundamentais: tal como cozer um bolo, uma temperatura demasiado elevada queimá-lo-á, uma temperatura demasiado baixa não o cozerá
Personalização dos parâmetros: diferentes materiais e componentes requerem diferentes "soluções de cozedura".
Seleção da pasta de solda: para escolher a fórmula especial para o grau aeroespacial, a pasta de solda comum simplesmente não consegue suportar o ambiente espacial
2. processamento de placa de circuito de grau de aviação
1. Controlo de precisão: a derradeira busca do nível de microns
Posicionamento por laser: precisão de ± 5 microns (equivalente a 1/10 de um cabelo)
Alinhamento ótico: Erro angular inferior a 0,001 graus (mais exato do que uma bússola)
Tratamento da superfície: folha de cobre com uma suavidade comparável à de um espelho (Ra≤0,3μm)
2. Verificação da fiabilidade: Testes mais rigorosos do que o ambiente espacial
Teste de tortura de temperatura: -65 ℃ a 150 ℃ repetidamente lançado 1000 vezes
Ensaio de vibração: simular a vibração violenta do lançamento de um foguetão
Teste de vácuo: 10-⁶ torr de vácuo sob o teste extremo
Ensaio de envelhecimento: 85 ℃ / 85% humidade sob a "sauna" contínua durante 1000 horas
3. controlo de qualidade
Monitorização do processo: monitorização em tempo real de cada parâmetro-chave, como um exame médico.
Sistema de rastreabilidade: cada placa tem um "cartão de identificação", e todo o processo pode ser rastreado.
Normas de certificação: cumprem as normas de qualidade mais rigorosas no sector da aviação (AS9100D, etc.)
4. processo especial
Processamento microporoso: Furos perfurados a laser mais finos do que um fio de cabelo (precisão de ±10μm).
Processamento de sinais de alta frequência: controlo de impedância com precisão de ±3% (comparável a instrumentos de laboratório)
Inspeção em três fases: auto-inspeção + inspeção + inspeção final, para garantir que nada se perde.
Acabamentos de superfície de PCBA aeroespacial ##
No ambiente espacial, as placas de circuitos enfrentam desafios muito superiores aos das aplicações terrestres. Para garantir um funcionamento fiável a longo prazo, devem ser utilizados "fatos de proteção" especiais:
1. Camada protetora de metal (tratamento anti-corrosão)
Níquel eletrolítico/ouro impregnado (ENIG): como uma "armadura dourada" para os circuitos, protege contra a ferrugem e garante uma boa condutividade.
Níquel eletrolítico/ouro (ENEPIG): "armadura composta" mais avançada, especialmente adequada para requisitos de elevada fiabilidade.
Caraterísticas: anti-oxidação, resistência à corrosão, para garantir que o contacto do conetor se mantém como novo.
2. camada protetora orgânica (proteção total)
Revestimento de poliimida (PI): "vestuário de proteção" de nível aeroespacial, resistência a altas temperaturas até 300 ℃ ou mais
Enchimento de silicone: circuitos sensíveis ao desgaste "airbag anti-vibração", amortecedor de choques mecânicos
Efeito: à prova de humidade, à prova de choque, à prova de radiação, proteção tripla num só passo.
Testes rigorosos de produtos
1. Teste de adaptabilidade ambiental
Corrida de resistência à temperatura:
Ciclo de temperatura alta e baixa (-65 ℃ ~ 150 ℃ lançamento repetido)
Choque de temperatura (comutação instantânea de temperaturas extremas)
Ensaio de resistência mecânica:
Ensaio de vibração (simular a vibração violenta de um lançamento de foguetão)
Teste de choque (choque de aceleração 1500G)
2. Verificação do desempenho elétrico
Teste da agulha voadora: como um "mestre acupunctor" para detetar com precisão cada nódulo
Verificação do suporte de teste: "Exame físico" exaustivo para garantir que todas as funções estão normais.
Integridade do sinal: análise da qualidade da transmissão de sinais de alta frequência
3. Ensaio de envelhecimento acelerado
Previsão de vida útil: Envelhecimento acelerado através de um ambiente de alta temperatura e alta humidade.
Monitorização contínua: registar a tendência dos parâmetros de desempenho
Análise de falhas: Utilizar um microscópio eletrónico para descobrir potenciais defeitos.
Em conclusão, os requisitos especiais do processo de PCBA aeroespacial reflectem-se na seleção de materiais, no processo de soldadura, no tratamento de superfícies, nas medidas de proteção e na verificação de testes, entre outros aspectos. Só seguindo rigorosamente estes requisitos e procedendo constantemente à inovação tecnológica e à melhoria dos processos é que podemos fabricar produtos PCBA que satisfaçam as necessidades do sector aeroespacial.