Flujo del proceso de montaje de PCB
Tabla de contenidos
¿Qué es el proceso de montaje de PCB?
Ensamblaje de PCB (Printed Circuit Board Assembly, PCBA) es el proceso completo de fabricación que consiste en montar componentes electrónicos en placas de circuitos impresos. Este procedimiento complejo y preciso implica múltiples pasos críticos, como la impresión de pasta de soldadura, la colocación de componentes, la soldadura por reflujo, la inspección de calidad, etc., transformando finalmente las placas desnudas en conjuntos electrónicos totalmente funcionales. A medida que los productos electrónicos tienden a la miniaturización y a un mayor rendimiento, los modernos procesos de montaje de placas de circuito impreso exigen requisitos cada vez más estrictos de precisión y fiabilidad.
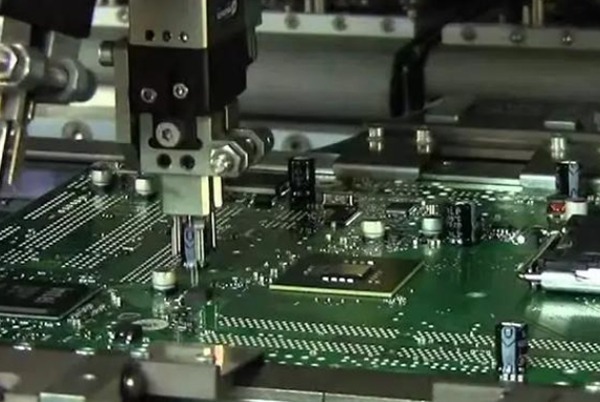
7 pasos clave en el proceso de montaje de placas de circuito impreso
1. Impresión de pasta de soldadura: El primer paso crítico para la precisión
La impresión de pasta de soldadura es el paso principal y más fundamental del montaje de placas de circuito impreso. Este proceso, similar a la serigrafía pero que requiere una mayor precisión, utiliza plantillas de acero inoxidable (normalmente de 0,1-0,15 mm de grosor).
Análisis de la composición de la pasta de soldadura:
La pasta de soldadura sin plomo moderna suele estar compuesta por:
- 96,5% Estaño (Sn)
- 3% Plata (Ag)
- 0,5% Cobre (Cu)
Esta combinación de aleaciones proporciona un excelente rendimiento de soldadura y resistencia mecánica. La pasta también contiene fundente, que elimina las capas de óxido de las superficies metálicas, reduce la tensión superficial de la soldadura y favorece el flujo y la humectación de la soldadura.
Proceso de impresión de precisión:
- La placa de circuito impreso se fija a la mesa de la impresora con fijaciones de precisión
- Las almohadillas del esténcil y de la placa de circuito impreso se alinean con precisión (normalmente se controla dentro de una tolerancia de ±25μm).
- La rasqueta se mueve en un ángulo adecuado (normalmente 60°) y ejerce presión (unos 5-10 kg) para empujar la pasta de soldadura a través de las aberturas del esténcil.
- Durante el desmoldeo, el esténcil se separa de la placa de circuito impreso, dejando pasta sólo en las almohadillas.
Puntos de control de calidad:
- Consistencia del espesor de la pasta de soldadura (medido con un medidor de espesor láser)
- Precisión de la posición de impresión
- Ausencia de puentes, soldadura insuficiente o picos.
2. Colocación de componentes SMT: "Pick and Place" de alta velocidad y precisión
Tras la impresión de la pasta de soldadura, la placa de circuito impreso entra en la línea de producción de tecnología de montaje en superficie (SMT), donde máquinas de colocación de alta velocidad colocan con precisión los componentes.
Tecnología moderna de máquinas de colocación:
- Precisión de colocación: ±25μm (los equipos de gama alta pueden alcanzar ±15μm)
- Velocidad de colocación: 30.000-150.000 componentes por hora
- Tamaño mínimo de los componentes: Puede manejar paquetes 01005 (0,4×0,2 mm) o más pequeños.
Flujo del proceso de colocación:
- Sistema de alimentación: Los componentes se suministran mediante cinta, tubos o bandejas
- Alineación por visión: Las cámaras de alta resolución identifican las marcas de referencia de las placas de circuito impreso
- Recogida de componentes: Las boquillas de vacío recogen los componentes de los alimentadores
- Inspección de componentes: Algunas máquinas disponen de cámaras para comprobar la polaridad, las dimensiones
- Colocación precisa: Los componentes se colocan sobre la pasta de soldadura según las coordenadas programadas
Principales factores de influencia:
- Precisión de alimentación de componentes
- Selección y mantenimiento de boquillas
- Estado de calibración de la máquina
- Control ambiental (normalmente 23±3°C, 40-60% HR)
3. Soldadura por reflujo: El perfil de temperatura determina la calidad de la soldadura
La soldadura por reflujo es el proceso crítico que funde la pasta de soldadura para formar conexiones eléctricas fiables, lo que requiere un control preciso del perfil de temperatura.
Perfil típico de temperatura de reflujo:
- Zona de precalentamiento: Rampa ascendente a 1-3°C/s hasta 150-180°C (activa el fundente)
- Zona de remojo: Mantener 140-180°C durante 60-90 segundos (iguala la temperatura de la PCB/componente).
- Zona de reflujo: Calentamiento rápido hasta alcanzar la temperatura máxima de 235-245°C (durante 30-60 segundos)
- Zona de enfriamiento: Enfriamiento controlado por debajo de 4°C/s (evita el choque térmico)
Comparación de tipos de hornos de reflujo:
- Horno de convección: Mejor uniformidad, adecuado para placas de circuito impreso complejas
- Horno de infrarrojos: Alta eficiencia de calentamiento, pero puede causar efectos de sombra
- Horno de fase vapor: Excelente uniformidad pero mayor coste, principalmente para productos militares.
PCB de doble cara Manipulación especial:
En las placas de circuito impreso SMT de doble cara, normalmente se suelda primero el lado con componentes más ligeros. Durante el segundo reflujo, asegúrese de que los componentes soldados previamente puedan soportar la temperatura.
4. Inspección de calidad: Múltiples defensas garantizan la fiabilidad
Tras la soldadura, las placas de circuito impreso se someten a rigurosas inspecciones de calidad:
4.1 Inspección visual manual
- Aplicaciones: Producción de bajo volumen, verificación de repeticiones
- Comprobaciones: Componentes ausentes/incorrectos, polaridad invertida, defectos evidentes de soldadura.
- Limitaciones: Baja eficiencia, propenso a la fatiga, sólo articulaciones visibles.
4.2 Inspección óptica automatizada (IOA)
- Principio: Las cámaras multiángulo de alta resolución comparan con muestras doradas
- Capacidades: Volumen de soldadura, puenteado, desalineación de componentes
- Ventajas: Rápido (normalmente 3-10 segundos/tabla), consistente
- Especificaciones: Resolución de 20μm, tasa de falsas alarmas <5%
4.3 Inspección por rayos X (AXI)
- Aplicaciones: BGA, QFN y otras juntas ocultas
- Capacidades: Integridad de la bola de soldadura, huecos, alineación de capas
- Sistemas: Rayos X 2D (menor coste), Rayos X 3D (tomografía)
Control estadístico de procesos (CEP):
Las fábricas modernas de PCBA retroalimentan los datos de inspección en tiempo real, utilizando métodos SPC para supervisar la estabilidad del proceso y evitar defectos en los lotes.
5. Ensamblaje de componentes pasantes: Tecnología tradicional en aplicaciones modernas
Aunque predomina la tecnología SMT, muchas placas de circuito impreso siguen necesitando componentes con tecnología de agujeros pasantes (THT), sobre todo conectores y dispositivos de alta potencia.
Dos métodos principales de soldadura:
5.1 Soldadura por ola
- Proceso: Inserción→fijación con pegamento→soldadura por ola→limpieza
- Tipos de olas: Onda simple (onda λ), onda doble (turbulenta+plana)
- Temperatura: Soldador mantenido a 250-260°C
- Aplicaciones: Placas de tecnología mixta de un solo lado de gran volumen
5.2 Soldadura selectiva
- Principio: Soldadura localizada para orificios pasantes específicos
- Ventajas: Impacto térmico mínimo, ideal para placas de doble cara
- Variantes: Soldadura láser, microondas, robots de soldadura
Fundamentos de la soldadura manual:
- Control de temperatura: 300-350°C en función del tamaño del componente
- Duración: 2-3 segundos por articulación para evitar daños
- Volumen de soldadura: Forma filetes cónicos de aproximadamente 45
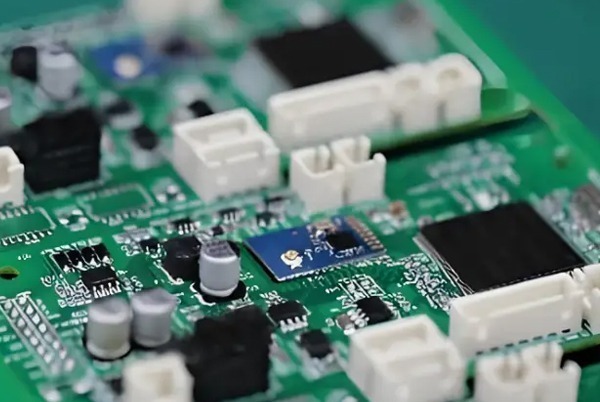
6. Pruebas funcionales: Verificación de la conformidad del diseño
Las pruebas funcionales son el último punto de control de la calidad y validan el rendimiento del producto.
Métodos de ensayo habituales:
6.1 Prueba en circuito (ICT)
- Utiliza un dispositivo "cama de clavos" para hacer contacto con los puntos de prueba
- Comprobaciones: Cortocircuitos, aperturas, valores de componentes, funciones básicas.
- Ventajas: Localización precisa de averías, pruebas rápidas
6.2 Prueba del circuito funcional (FCT)
- Simula las condiciones reales de funcionamiento
- Introduce señales de prueba, verifica las salidas
- Puede integrarse con la automatización para pruebas 100%
6.3 Prueba de exploración de límites
- Para PCB de alta densidad e inaccesibles
- Utiliza interfaz JTAG
- Ideal para dispositivos programables (FPGA, CPLD)
Análisis de la cobertura de las pruebas:
Unos planes de pruebas excelentes deben cubrir >90% de modos de fallo potenciales, optimizados mediante el Análisis Modal de Fallos y Efectos (AMFE).
7. Limpieza y protección: Claves para la longevidad del producto
Las elevadas exigencias de fiabilidad de la electrónica moderna hacen que la limpieza sea cada vez más crítica.
Opciones del proceso de limpieza:
7.1 Limpieza acuosa
- Utiliza agua desionizada (resistividad >1MΩ-cm)
- Puede añadir agentes de limpieza ecológicos
- Apto para la mayoría de los aparatos electrónicos convencionales
7.2 Limpieza con disolventes
- Utiliza alcohol o disolventes de hidrocarburos
- Gran capacidad de limpieza, secado rápido
- Requiere precauciones de seguridad y medioambientales
7.3 Proceso sin limpieza
- Utiliza pasta de soldar de bajo residuo y sin necesidad de limpieza
- Debe seguir cumpliendo las normas de limpieza iónica (<1,56μg/cm² equivalente de NaCl).
Revestimiento conforme:
Para aplicaciones en entornos difíciles:
- Acrílico: Fácil aplicación y repaso
- Poliuretano: Excelente resistencia química
- Silicona: Rendimiento superior a altas temperaturas
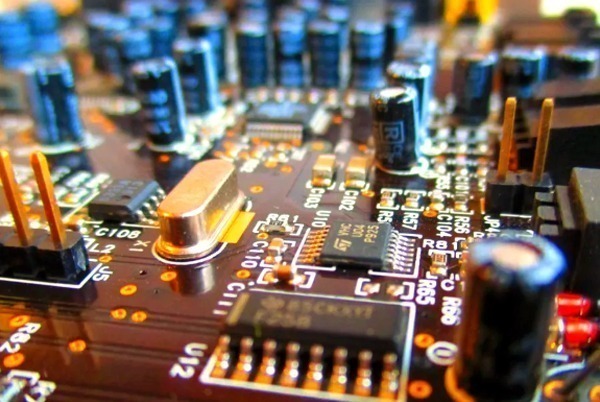
Tendencias modernas en el montaje de PCB
Tecnología de interconexión de alta densidad (HDI)
- Líneas más finas (<50μm)
- Tecnología de microvías (vías ciegas/enterradas)
- Interconexión a cualquier nivel
Fabricación de electrónica flexible
- Montaje de sustrato flexible
- Montaje en superficies curvas 3D
- Circuitos electrónicos extensibles
Transformación de la fabricación inteligente
- Aplicaciones del gemelo digital
- Inspección de calidad basada en IA
- Sistemas de producción adaptables
Requisitos para una fabricación ecológica
- Materiales sin plomo ni halógenos
- Procesos energéticamente eficientes
- Reciclado de residuos
Problemas comunes de montaje de PCB y soluciones
Tipo de problema | Posibles causas | Soluciones |
---|---|---|
Puentes de soldadura | Mal diseño del esténcil, exceso de pasta | Optimización de las aberturas de los esténciles, ajuste de los parámetros de impresión |
Soldadura en frío | Poca actividad pastosa, perfil inadecuado | Cambiar la pasta, optimizar la curva de reflujo |
Tombstoning | Diseño de almohadilla asimétrica, calentamiento desigual | Optimizar el diseño de los pads, ajustar el reflujo |
Bolas de soldadura | Pasta oxidada, alta humedad | Controlar la humedad, reducir la exposición a la pasta |
Huecos BGA | Desgasificación de la pasta, calentamiento rápido | Seleccione pasta de bajo contenido en vacíos, optimice el precalentamiento |
Conclusión
El montaje de PCB es el proceso de fabricación crítico que transforma los diseños en productos físicos, integrando la ciencia de los materiales, la mecánica de precisión, la automatización y mucho más. A medida que la electrónica se hace más compleja, los procesos modernos de PCBA evolucionan hacia una mayor precisión, eficiencia e inteligencia. Dominar todo el flujo de trabajo de ensamblaje y los puntos de control clave es esencial para garantizar la calidad y la productividad. Tanto en la producción en serie como en la de bajo volumen y alta mezcla, sigue siendo fundamental seleccionar las rutas de proceso y los métodos de calidad adecuados en función de las características del producto.
Entradas relacionadas