La tecnología de montaje superficial (SMT) representa el núcleo del ensamblaje electrónico moderno, ya que transforma los tradicionales componentes discretos con orificios pasantes en dispositivos compactos de chip sin plomo o con plomo corto montados directamente en las superficies de las placas de circuitos impresos. Esta tecnología permite ensamblar productos electrónicos de alta densidad, gran fiabilidad, miniaturizados y rentables, al tiempo que admite procesos de fabricación automatizados.
Tecnología de montaje superficial
La tecnología de montaje superficial (SMT) ha revolucionado la fabricación electrónica moderna al sustituir los voluminosos componentes con orificios pasantes por dispositivos de chip compactos y sin plomo que se montan directamente en placas de circuitos impresos. Como proceso de montaje dominante en la industria, la SMT permite la producción automatizada de dispositivos electrónicos de alta densidad, ultrafiables y miniaturizados a costes reducidos. Esta tecnología transformadora se ha convertido en omnipresente en sistemas informáticos, equipos de comunicación e innumerables productos electrónicos, y su adopción sigue creciendo a medida que disminuye el uso de componentes tradicionales con orificios pasantes. Los continuos avances de los procesos y componentes SMT la han consolidado como el estándar de oro en el ensamblaje electrónico, impulsando la innovación y satisfaciendo la creciente demanda de dispositivos electrónicos más pequeños, potentes y rentables en todos los sectores del mercado.
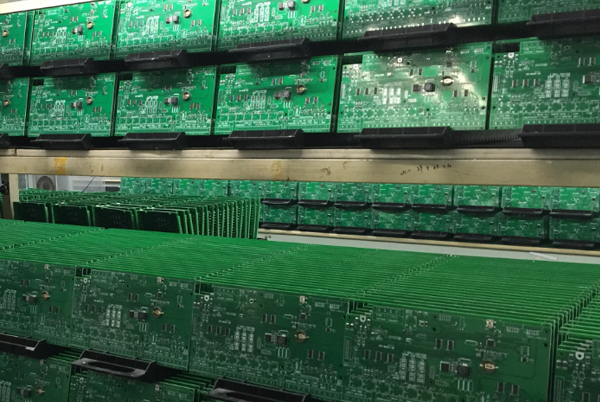
Evolución y antecedentes técnicos de SMT
Contexto del desarrollo tecnológico
Las tendencias hacia una electrónica inteligente, multimedia y en red han impulsado tres requisitos básicos para la tecnología de ensamblaje: alta densidad, alta velocidad y estandarización. Estas exigencias impulsaron el revolucionario cambio de la tradicional tecnología de taladro pasante (THT) a la tecnología de montaje en superficie.
Historia del desarrollo mundial
La tecnología SMT se originó en la década de 1960 y ha pasado por cuatro fases fundamentales:
- Exploración inicial (años 70): Se utiliza principalmente en circuitos integrados híbridos y productos de consumo como relojes electrónicos y calculadoras.
- Rápido crecimiento (mediados de los 80): Madurez creciente y aplicaciones ampliadas
- Adopción generalizada (década de 1990): Se convirtió en la principal tecnología de ensamblaje, sustituyendo gradualmente al THT.
- Innovación continua (siglo XXI-actualidad): Mayor densidad, menor tamaño y mejores prestaciones
Situación actual en China
La tecnología SMT se introdujo en China en la década de 1980, inicialmente para la producción de sintonizadores de televisión, antes de extenderse a la electrónica de consumo, como videograbadoras y cámaras. Desde 2000, con el rápido desarrollo de la industria electrónica de la información, las importaciones de equipos SMT han crecido sustancialmente, estableciendo a China como la mayor base mundial de fabricación de SMT.
Principales ventajas de la tecnología SMT
- Montaje de alta densidad: Reduce el volumen del producto en 60% y el peso en 75%
- Fiabilidad excepcional: Tasas de defectos en las juntas de soldadura un orden de magnitud inferiores a las del THT, con una resistencia superior a los golpes.
- Excelentes características de alta frecuencia: Minimiza la capacitancia e inductancia parásitas al tiempo que reduce las interferencias electromagnéticas.
- Automatización eficiente: Simplifica los procesos de producción y mejora la eficacia
- Importantes ventajas económicas: Reduce los costes totales de producción en un 30-50%
Principales tendencias tecnológicas en SMT
Innovaciones en el embalaje de componentes
La tecnología de envasado sigue evolucionando hacia tamaños más pequeños, más E/S y mayor fiabilidad, con tendencias importantes como:
- Integración de módulos multichip (MCM)
- Desarrollo de redes de resistencias de chip
- Tecnología de sistema en paquete (SiP)
- Integración de sistemas en chip (SoC)
- Aplicaciones de silicio sobre aislador (SOI)
- Investigación sobre dispositivos nanoelectrónicos
Avances en los equipos de producción
Los equipos SMT modernos avanzan hacia la eficiencia, la flexibilidad y la sostenibilidad medioambiental:
- Alta eficacia: La doble vía de alimentación de placas y los diseños multicabezal aumentan la productividad
- Sistemas inteligentes: La inspección por visión y los controles digitales mejoran la precisión y la velocidad
- Configuraciones flexibles: Los diseños modulares se adaptan a diversas necesidades de producción
- Soluciones ecológicas: Reducción del ruido y control de la contaminación para una fabricación ecológica
Innovaciones tecnológicas en placas de circuitos
Tendencias de desarrollo de las placas de montaje superficial (SMB):
- Alta precisión: 0,06 mm de ancho de línea, 0,08 mm de espaciado
- Alta densidad: apertura mínima de 0,1 mm
- Diseños ultrafinos: Placas de 6 capas de 0,45-0,6 mm de grosor
- Fabricación de placas multicapa: Interconexiones de alta densidad de 30-50 capas
- Aumento de las aplicaciones de cartón flexible
- Uso generalizado de sustratos cerámicos
- Tecnologías de revestimiento de superficies sin plomo
Componentes básicos de los procesos SMT
Tipos de procesos primarios
- Soldadura por reflujo: Sencillo y eficaz para productos miniaturizados
- Soldadura SMT-Wave: Combina componentes con orificios pasantes y de montaje en superficie
- Pasta de Soldadura de Doble Cara-Reflujo: Permite un ensamblaje de muy alta densidad
- Montaje híbrido: Integra múltiples ventajas tecnológicas
Procesos clave de la línea de producción
- Impresión de pasta de soldadura: Aplicación precisa en placas de circuito impreso
- Colocación de componentes: Montaje de SMD de alta precisión
- Soldadura reflow: Crea conexiones eléctricas fiables
- Limpieza e inspección: Elimina residuos y verifica la calidad
Tres detalles críticos del proceso
- Aplicación de la pasta: Impresión automatizada o semiautomatizada para una distribución uniforme
- Colocación de componentes: Posicionamiento a nivel de micras mediante sistemas de colocación de precisión
- Soldadura reflow: Perfilado preciso de la temperatura para una soldadura óptima
Gestión de la protección contra descargas electrostáticas (ESD)
Riesgos de ESD
La electricidad estática puede causar daños inmediatos o latentes en los componentes electrónicos, siendo los defectos latentes responsables de 90% de los fallos y suponiendo importantes amenazas para la calidad.
Medidas de protección
- Sistemas de protección personal: Muñequeras, prendas y calzado antiestáticos
- Controles medioambientales: Suelos y superficies de trabajo a prueba de ESD
- Protocolos operativos: Estrictos procedimientos de gestión de la ESD en las zonas de producción
Detalles de la tecnología de proceso SMT de tres núcleos
1. Proceso de aplicación de la pasta de soldadura
Como primer proceso crítico en las líneas de producción SMT, la calidad de la aplicación de la pasta de soldadura afecta directamente a las operaciones posteriores. La impresión moderna de pasta de soldadura utiliza principalmente la tecnología de impresión por esténcil, con aspectos técnicos clave como:
- Equipos de impresión:
- Las impresoras totalmente automáticas con sistemas de alineación por visión alcanzan una precisión de posicionamiento de ±12,5μm
- Los modelos semiautomáticos se adaptan a la producción de lotes medianos/pequeños
- Control de procesos:
- El ángulo de la escobilla de goma suele mantenerse entre 45 y 60°.
- Velocidad de impresión controlada entre 20-80mm/s
- Presión de impresión mantenida entre 5 y 15 kg
- Diseño de plantillas:
- Selección de grosor: 0,1-0,15 mm para componentes estándar, 0,08 mm para paso fino
- Diseño de apertura: La relación de área >0,66 garantiza una liberación adecuada de la pasta
- Gestión de la pasta:
- Requiere un reacondicionamiento mínimo de 4 horas antes de su uso
- Con 2-3 minutos de mezcla se consigue una viscosidad óptima
- Condiciones ambientales: 23±3°C, 40-60% RH
2. Tecnología de colocación de componentes
El núcleo de la fabricación SMT, las modernas máquinas de colocación ofrecen un montaje automatizado ultrapreciso:
- Tipos de equipos:
- Colocadores de alta velocidad: Hasta 250.000 CPH para componentes pequeños
- Máquinas multifunción: Manipulación de componentes de formas extrañas con una precisión de ±25μm.
- Sistemas modulares: Configuraciones flexibles para necesidades diversas
- Parámetros técnicos críticos:
- Precisión de colocación: ±30μm@3σ (las máquinas de gama alta alcanzan ±15μm)
- Tamaño mínimo del componente: 0201 (0,25×0,125 mm) o inferior
- Reconocimiento de componentes: CCD de alta resolución (hasta 0,01 mm/píxel)
- Controles de procesos clave:
- Selección y mantenimiento de boquillas
- Calibración del alimentador
- Control de la fuerza de colocación (10-500g ajustable)
- Calibración del sistema de alineación de visión
3. Proceso de soldadura por reflujo
El proceso crítico para conseguir uniones soldadas fiables requiere un control preciso de la temperatura:
- Perfil de temperatura Zonas:
- Precalentamiento: Ambiente→150°C a una velocidad de rampa de 1-3°C/s
- Remojo: 150-180°C durante 60-90 segundos
- Reflujo: Temperatura pico 220-245°C durante 30-60 segundos
- Enfriamiento: Ritmo <4°C/s
- Tipos de equipos:
- Reflujo por convección: Excelente uniformidad de temperatura
- Reflujo infrarrojo: Alta eficiencia térmica
- Sistemas híbridos: Combinan ambas ventajas
- Controles de procesos críticos:
- Contenido de oxígeno (<1000ppm)
- Velocidad de transporte (0,8-1,5 m/min)
- Colocación y control de termopares
- Optimización del perfil para diferentes pastas
- Prevención de defectos comunes:
- Tombstoning: Optimizar el diseño de la plataforma, controlar la velocidad de rampa
- Puentes: Ajuste de las aberturas de la pantalla, parámetros de la racleta
- Juntas frías: Garantizar una temperatura de pico/duración adecuada
Estos tres procesos constituyen el núcleo tecnológico de la fabricación SMT. Cada uno de ellos requiere un control preciso de los procesos y una estricta gestión de la calidad para garantizar la fiabilidad y consistencia del producto final. Las líneas SMT modernas utilizan sistemas MES para supervisar todos los datos del proceso y garantizar la trazabilidad de los parámetros y la estabilidad del proceso.