Descripción
En la fabricación electrónica moderna, la calidad del montaje industrial de placas de circuito impreso determina directamente el rendimiento y la fiabilidad del producto final. Como proveedor integral de soluciones de PCB con 17 años de experiencia en el sector, conocemos a fondo los estrictos requisitos de las aplicaciones industriales para el montaje de placas de circuito impreso: desde la fiabilidad absoluta para dispositivos médicos hasta la estabilidad a largo plazo para sistemas de control industrial, y desde la adaptabilidad medioambiental para electrónica de automoción hasta el rendimiento extremo para grado aeroespacial. Este artículo explorará las tecnologías clave, el control de calidad y las aplicaciones industriales del ensamblaje industrial de placas de circuito impreso, mostrando cómo la fabricación electrónica moderna consigue el equilibrio perfecto entre funcionalidad y fiabilidad mediante procesos de precisión.
Principales ventajas tecnológicas del montaje industrial de PCB
En la industria electrónica de rápido crecimiento, el montaje industrial de PCB ha evolucionado desde el simple montaje de componentes a un proyecto sistemático que integra la ciencia de los materiales, la maquinaria de precisión y el control de automatización. Las líneas de producción SMT totalmente automatizadas construidas en nuestras fábricas pueden lograr una calidad constante para millones de uniones soldadas por hora, gracias a la sinergia de tres pilares tecnológicos fundamentales.
1. Tecnología de montaje de alta precisión
Es la primera barrera de calidad para el montaje industrial de placas de circuito impreso. Nuestra máquina de colocación multifuncional está equipada con un sistema de posicionamiento por visión submicrónica, que puede manejar con precisión diversos requisitos de componentes que van desde componentes ultraminiatura 01005 (0,4 mm x 0,2 mm) a grandes BGA (45 mm x 45 mm). En la producción real, la precisión de colocación alcanza ±25μm (CPK≥1,67), y el desplazamiento del componente se controla estrictamente dentro de 15% de la anchura de la almohadilla, que es mucho mejor que el requisito estándar de la industria de 25%. Esta precisión garantiza la integridad de la transmisión de señales de alta frecuencia y el rendimiento de disipación térmica de los dispositivos de potencia.
2. Sistemas inteligentes de control del proceso de soldadura
Forma la base para una conexión eléctrica fiable. Nuestro horno de reflujo blindado con nitrógeno de 10 zonas de temperatura está equipado con un sistema de seguimiento de temperatura en tiempo real que optimiza automáticamente el perfil de temperatura para diferentes aleaciones de pasta de soldadura (SAC305, SnBi58, etc.) y materiales de PCB (alto TG, sustratos cerámicos, etc.). Los datos reales muestran que el sistema puede controlar la tasa de defectos de soldadura a <200DPPM (defectos por millón de puntos), especialmente en QFN, LGA y otros componentes de almohadilla inferior con un rendimiento de soldadura de 99,98% o superior.
3.Sistema tecnológico de inspección 3D
Se realiza un control de bucle cerrado de la calidad del proceso. SPI (Inspección de pasta de soldadura), AOI (Inspección óptica automática) y rayos X 3D desplegados en la línea de producción forman el "Triángulo de calidad": El sistema SPI supervisa la desviación del grosor de la pasta de soldadura con una resolución de 5μm; el equipo AOI reconoce las anomalías de las juntas de soldadura con una profundidad de 0,02mm² mediante el algoritmo de aprendizaje profundo; y los rayos X pueden visualizar la conexión interna de la placa de circuito impreso de 56 capas. Esta estrategia de inspección multicapa ha dado como resultado una tasa de detección 98% de problemas de proceso tempranos, reduciendo drásticamente los costes de reparación posteriores.
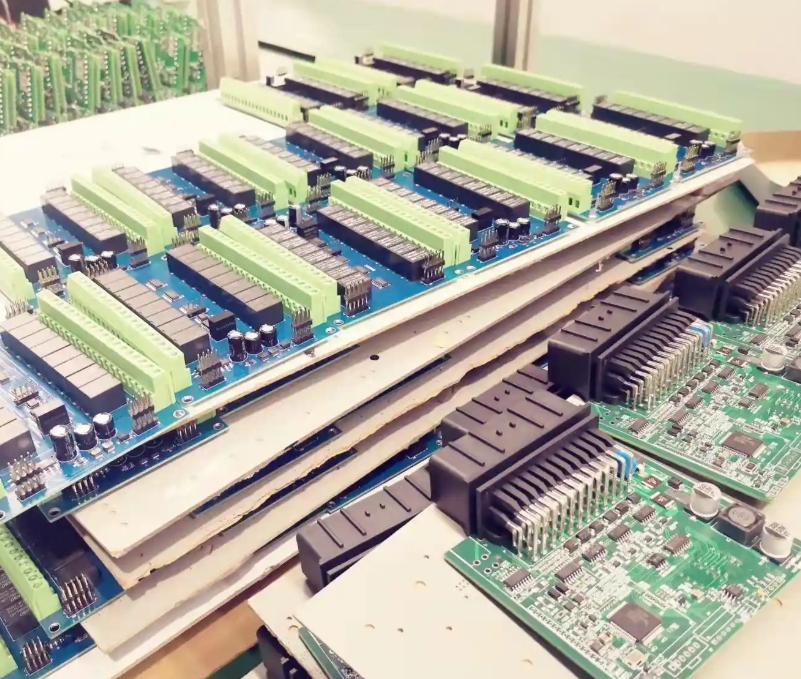
Capacidades completas de fabricación por procesos, desde el diseño hasta la prueba
La fiabilidad de los dispositivos electrónicos industriales comienza en la fase de diseño, continúa en el proceso de fabricación y finaliza con las pruebas. Nuestro **sistema de fabricación de ciclo de vida completo** cubre todos los puntos críticos, desde la asistencia al diseño hasta la producción en serie, garantizando que los componentes PCB mantengan un funcionamiento estable a largo plazo en entornos industriales adversos.
1. Fase de cooptimización del diseño
Nuestro equipo de ingenieros interviene con antelación en el proceso de diseño del cliente para ofrecer recomendaciones de análisis de fabricabilidad (DFM) y diseño para fiabilidad (DFR). Gracias a un software de simulación específico, podemos identificar problemas de adaptación de impedancias en líneas de señal de alta velocidad, predecir la distribución del calor en el plano de potencia y proponer soluciones de optimización. Hemos ayudado a un cliente de controladores industriales a reducir el número de iteraciones de diseño de 5 a 2, acortando el ciclo de desarrollo en 40%. Esta colaboración previa reduce significativamente los riesgos de calidad en la producción posterior.
2. Línea de producción flexible
Las líneas de producción flexibles pueden responder simultáneamente a necesidades de producción diversificadas: las líneas SMT de doble carril permiten un cambio de línea rápido (<15 minutos) y admiten una producción flexible desde prototipos hasta volúmenes medios (50-10.000 piezas); el equipo de soldadura por ola selectiva puede controlar el rango de choque térmico de los componentes de orificio pasante más allá de 5 mm de los componentes vecinos; el proceso de revestimiento triple antipreventivo controla con precisión el grosor del revestimiento entre 25-75μm para satisfacer los requisitos de diferentes niveles de protección. El proceso de revestimiento triple antipreventivo controla con precisión el grosor del revestimiento entre 25-75μm para satisfacer los requisitos de diferentes niveles de protección. Esta capacidad de producción flexible nos permite atender a clientes de distintos campos, como equipos médicos y automatización industrial, sin sacrificar la eficiencia de la producción ni los estándares de calidad.
3. Sistema de verificación de la fiabilidad
El sistema de verificación de la fiabilidad es la principal ventaja que nos distingue de la competencia. Ensamblaje de PCB fábricas. Además de las pruebas convencionales ICT (in-circuit test) y FCT (functional test), hemos creado un completo laboratorio Environmental Stress Screening (ESS) que puede realizar:
- Prueba de ciclos de temperatura (-55℃~+125℃, 100 ciclos)
- Almacenamiento a alta temperatura y humedad (85℃/85%RH, 1000 horas)
- Prueba de vibración mecánica (5-500 Hz, 30 minutos para cada uno de los 3 ejes)
- Prueba de ciclo de alimentación (carga 0-100%, 10.000 veces)
Estas rigurosas pruebas garantizan la fiabilidad a largo plazo de los productos en entornos industriales. El cuadro de control de un proyecto de transporte ferroviario ha logrado más de 50.000 horas de funcionamiento sin fallos sobre el terreno tras superar las pruebas.
Procesos industriales especializados y soluciones de materiales
Los dispositivos electrónicos industriales a menudo se enfrentan a desafíos medioambientales extremos, como altas temperaturas, alta humedad, vibración y corrosión, que son difíciles de superar con los procesos de montaje de PCB comunes para el consumidor. Hemos desarrollado **Sistemas de procesos especializados** que se especializan en estas duras condiciones y ofrecen soluciones fiables para aplicaciones críticas.
1. Tecnología de soldadura de alta fiabilidad
Hemos desarrollado diversas soluciones para distintos escenarios de aplicación
- La tecnología Copper Wire Bonding (CWB) se utiliza para conexiones de alta corriente, sustituyendo a los métodos tradicionales de unión de cables y aumentando la capacidad de transporte de corriente hasta 300%.
- Sinterizado Ag para el montaje de módulos de potencia con temperaturas de funcionamiento de hasta 200°C.
- La soldadura a baja temperatura (SnBi58) se utiliza para componentes sensibles al calor, y la ventana de proceso se controla dentro de ±3℃.
Estos procesos han aumentado el MTBF (tiempo medio entre fallos) de un módulo de carga de vehículo eléctrico de 50.000 horas a 150.000 horas.
2. Capacidad de procesamiento de sustratos especiales
Satisfacer las exigencias de diversas aplicaciones complejas
- Tecnología de procesamiento de PCB de cobre grueso (6 oz de espesor de cobre) para soportar el diseño de fuentes de alimentación industriales de alta corriente.
- Proceso de moldeo integrado Rigid-Flex para reducir los puntos de fallo de los conectores
- Tratamiento de la conductividad térmica del sustrato metálico (IMS), para resolver el problema de la disipación del calor de los LED de alta potencia.
- Procesamiento de precisión de materiales de alta frecuencia (Rogers, Tecneli), para garantizar el rendimiento de RF de las estaciones base 5G.
3. Para la corrosión química en entornos industriales
Ofrecemos un programa de protección multinivel
- Tecnología de nanorrevestimiento para formar una película protectora de 5-8μm que supera una prueba de niebla salina de 96 horas.
- Proceso de revestimiento conformado para conseguir una protección a prueba de tres factores (humedad, moho y niebla salina).
- La tecnología de encapsulado se utiliza para que los equipos subacuáticos alcancen un nivel de protección IP68.
Tras adoptar estas tecnologías de protección, la tasa de fallos del equipo de vigilancia oceánica en un entorno de niebla salina se redujo en 90%.

Ejemplos de aplicaciones industriales e innovación tecnológica
El verdadero valor de la tecnología de montaje industrial de PCB reside en su capacidad para resolver problemas específicos de la industria. A través de los siguientes casos típicos, podrá comprender cómo combinamos la tecnología de fabricación avanzada con las necesidades de la industria para crear soluciones prácticas.
1. Automatización industrial
Un fabricante de PLC (controladores lógicos programables) de una marca internacional se enfrentaba a una elevada tasa de fallos de sus productos sobre el terreno. Aportamos una solución integral mediante la optimización de la integridad de la señal y el diseño de protección contra vibraciones:
- Control de impedancia (±7%) de la placa base HDI de 24 capas para reducir la fluctuación de señal en 42%.
- Mejora de la fiabilidad de las uniones soldadas BGA con la tecnología Via-in-Pad.
- Desarrollo de dispositivos antivibración especializados para reducir la tensión durante la producción en un 60%.
Tras la implantación, la tasa de fallos de campo del producto se redujo de 1,8% a 0,15%, lo que redujo las pérdidas del cliente en unos 2 millones de dólares al año.
2. Aplicación de equipos médicos
Proporcionamos componentes de PCB de ruido ultrabajo para un dispositivo de imagen médica de gama alta:
- Utilización de materiales de pérdidas ultrabajas (Dk=3,3±0,05)
- Implementación de una estructura laminar híbrida para controlar el coeficiente de expansión térmica (CTE).
- Proceso de limpieza especial desarrollado para controlar los residuos iónicos a <0,3μg/cm².
En definitiva, la relación señal-ruido (SNR) del equipo mejora con 35%, y la precisión de detección alcanza los 0,1 mm.
3. Nuevo campo energético
Un fabricante de inversores fotovoltaicos se encontró con un fallo prematuro de los módulos de potencia. La solución de optimización de la gestión térmica que propusimos incluía:
- Diseño de una estructura 3D de disipación de calor con 55% de menor resistencia térmica
- Aplicación del sustrato de soldadura fuerte de metal activo (AMB)
- Vacíos de soldadura optimizados <5% (15% típico del sector)
Solución que prolonga la vida útil del producto de 5 a 10 años a 70 °C de temperatura ambiente.
4. En Electrónica del Automóvil
Desarrollamos un sistema de fabricación para automoción que cumple las normas AEC-Q100:
- Establecimiento de un proceso de ensayo de tensión de compuestos de temperatura y vibración
- Implantación de un sistema de trazabilidad de la cadena de suministro.
- Proceso de conexión desarrollado resistente a altas temperaturas (150℃ de funcionamiento continuo).
Hemos proporcionado servicios de producción en serie para más de 30 tipos de ECU de automoción, y hemos entregado más de 5 millones de piezas de productos sin defectos.
Un ecosistema tecnológico para la innovación continua
En un entorno tecnológico en rápida evolución, el ensamblaje industrial de PCB debe romper constantemente los límites existentes. La plataforma de innovación colaborativa industria-universidad-investigación que hemos construido sigue promoviendo el avance tecnológico de la industria y resolviendo los retos a los que se enfrentará la fabricación electrónica en el futuro.
1. Tecnología avanzada de integración de envases
- La tecnología SiP (System-in-package) integra varios chips en un único encapsulado, lo que permite reducir el tamaño de un módulo de sensores en 70%.
- Los componentes integrados en la placa de circuito impreso (EDP) serán componentes pasivos enterrados en la placa para mejorar la fiabilidad
- Capacidades de procesamiento de envases a nivel de oblea (WLP) para apoyar la integración de una nueva generación de sensores.
2. Sistema Digitalizado de Fabricación Inteligente (DIMS)
- El sistema MES controla más de 200 parámetros de proceso en tiempo real
- Cada PCB tiene un identificador único y 15 años de conservación de datos.
- El análisis de big data predice el calendario de mantenimiento de los equipos, lo que reduce el tiempo de inactividad en 30%.
3. Tecnología de fabricación ecológica
- El proceso de soldadura sin plomo cumple la normativa RoHS 2.0.
- La tasa de reciclado de residuos aumentó a más de 95%.
- Desarrollo de un proceso de fabricación a baja temperatura para reducir el consumo de energía en 40%.
Mediante asociaciones estratégicas con proveedores mundiales de materiales, fabricantes de equipos e instituciones de investigación, seguimos convirtiendo tecnologías punteras en soluciones de fabricación utilizables industrialmente. Por ejemplo, la recientemente desarrollada **Tecnología de Integración Fotónica** se ha aplicado con éxito a la producción de módulos ópticos para estaciones base 5G, mejorando la precisión de la alineación óptica hasta el nivel de ±1μm.
¿Por qué elegir Topfast?
El montaje industrial de PCB es un arte del equilibrio: encontrar la solución óptima entre precisión y eficacia, innovación y madurez, coste y fiabilidad. 17 años, siempre nos hemos adherido a un principio: la calidad de los productos electrónicos industriales no sólo está relacionada con la reputación de la empresa, sino también con la seguridad y la estabilidad del sistema del usuario final.
Desde dispositivos médicos para salvar vidas hasta sistemas de automatización industrial para garantizar la seguridad de la producción, pasando por la electrónica del automóvil para proteger la seguridad de la conducción o los sistemas energéticos para mantener la estabilidad de la red: cada placa de circuito impreso ensamblada por nosotros conlleva una importante misión. Esta es la motivación fundamental que nos impulsa a invertir en equipos de última generación (inversión acumulada de más de 30 millones de dólares), cultivar un equipo profesional (técnicos con una media de 12 años de experiencia en el campo) y mejorar el sistema de calidad (certificado por ISO9001, IATF16949, etc.).
En el futuro, con la popularización de la Industria 4.0 y las tecnologías AIoT, la electrónica industrial se enfrentará a retos de integración más complejos y a requisitos medioambientales más estrictos. Seguiremos profundizando en nuestra tecnología de fabricación de precisión a la vez que ampliamos nuestras capacidades de soluciones a nivel de sistema para proporcionar soporte técnico completo desde el diseño de PCB, la fabricación y el montaje a nuestros clientes industriales globales, y para promover conjuntamente la mejora continua de los estándares de fiabilidad de los componentes electrónicos clave.